Sustainable aviation fuel is seen as having great potential to reduce the greenhouse gas emissions from air transportation. However, as with other emerging renewable energy sources, the safety risks arising from the production, processing and storage of these biofuels can be accompanied by new risks and will require careful management from the safety industry as utilisation increases to meet the Government’s mandatory targets.
Features
Sustainable aviation fuels: how do we put the SAFety in SAF?
The topic of sustainable aviation fuel (SAF) has been garnering increasing attention over recent years. Currently used as a partial replacement for conventional jet fuel, it is a form of biofuel made from waste products, such as used cooking oil, algae, biowaste and other forms of municipal waste, and which offers significant potential to reduce greenhouse gas emissions.
SAF was brought into sharp focus at the beginning of the year following the introduction of the UK Government’s SAF Mandate, which came into effect on 1 January. The Mandate requires greater use of sustainable aviation fuels to secure a growing demand for SAF by:
- Obligating the supply of an increasing amount of SAF in the overall UK aviation fuel mix; and
- Incentivising SAF supply through the award of tradeable certificates with a cash value.
Over the coming years, the percentage of SAF as a total of UK jet fuel will steadily increase, starting at two per cent this year, reaching 10 per cent by 2030 and increasing to 22 per cent by 2040. It is hoped that the use of SAF could deliver up to 6.3 mega tonnes of carbon savings per year by 2040.
The percentage of sustainable aviation fuel as a total of UK jet fuel will increase to 22 per cent by 2040. Photograph: Draeger
This is a significant development for UK industry, affecting not just the fuel and aviation sector, but those industries further down the supply chain, such as those involved in the production, processing and storage of biomass and biowaste. In many instances, SAF innovation will rely on novel applications of existing processes, but it will also involve new and lesser-known processes and innovation, leading to a variety of safety challenges across the industry.
The Government’s new Mandate makes it clear that safety standards must not be compromised when introducing new decarbonisation technologies, and this is an important baseline premise.
The importance of safety keeping pace in the broader energy transition is a topic that Dräger has highlighted for some time now, and it applies to many areas of new energy innovation, from SAF and energy from waste to use of hydrogen as a biofuel. Furthermore, ambitious timescales mean that it is all the more imperative that safety is built in at an early stage to ensure the industry gets safety right first time.
Gas safety considerations
Gas safety is a key safety consideration relating to SAF and is a useful example to explore to better illustrate and understand the challenges involved.
It is perhaps inevitable that there will be unknowns and uncertainties in the early stages of new innovations, but in some respects, many of the gas safety considerations related to SAF are not dissimilar to those seen elsewhere in wider industry. For example, good gas detection and monitoring has been a cornerstone of safe operations in industries such as wastewater treatment or chemical processing for decades.
The Government’s new mandate makes it clear that safety standards must not be compromised when introducing new decarbonisation technologies. Photograph: Draeger
The key difference when it comes to SAF is the combination of new applications, new processes, frequently new people working in an early-stage industry, and the creation of new safety processes and protocols. In emerging industries, it’s vital that the knowledge and experience gained through more established sectors (such as oil and gas or the chemical industries) is borne in mind and applied wisely wherever appropriate.
Pathways to sustainable aviation fuel
There are three recognised pathways to produce sustainable aviation fuel. These are:
1. HEFA (hydro-processed esters and fatty acids), which is a fuel developed from oils or fats, such as used cooking oil.
2. Non–HEFA – which includes several different methods of making advanced fuels from wastes and residues, such as fuel made from municipal solid waste.
3. Power to liquid – this is a relatively new technique which provides a promising and scalable fuel for the future. The process combines carbon dioxide, water and renewable energy to produce SAF with properties that are similar to conventional jet fuel. The three major steps that comprise this pathway are carbon capture, hydrogen production and hydrocarbons synthesis.
HEFA and Non–HEFA
These techniques are the most widely adopted and currently provide the only commercially viable technology, and it is believed that this will enable the UK to reach the first 2030 threshold for SAF.
However, there is a lack of aromatics in HEFA feedstocks. These aromatics are reactive molecules which are needed for maintaining seal compatibility. Fuel-seal compatibility is, unsurprisingly, an important consideration for SAF certification and blending limits so it is not advisable to use more than 50 per cent HEFA SAF to maintain the required fuel characteristics and maintain the long-term health of the aircraft engine.
The production of HEFA SAF involves the hydrotreatment of organic feedstocks, such as vegetable oils, fats and greases, in order to create a fuel that is compatible with existing aviation infrastructure and aircraft technologies.
Megan Hine: "We are already working closely with companies developing new SAF technologies."
The good news is that many of the risks are well understood in processing heavy hydrocarbons. The supply chain is sufficiently mature to provide comprehensive safety solutions for application of hydrocarbon substances and volatile organic compounds (VOCs). These solutions include flame and gas detection systems, as well as personal protective and detection equipment, such as respiratory protection or personal portable gas monitors.
There will however be changes to how we handle this kind of waste and the touch points in industry. There will need to be consideration given to how much of the waste is processed on the waste generating site, or whether it will be transported, unprocessed, to a different site for the refining process to begin.
If new plant and equipment is installed as part of the process, associated fire and gas detection will need to meet current safety guidelines, such as BS (British Standard) 60080:2020, which may not have existed when the original plant was built.
Meanwhile, non-HEFA technology converts waste material which, as is the case with landfill sites, carries the risk of exposure to methane gas. This technology also relies on the use of biomass waste which has significant fire and explosive gas hazards, as well as hazards from exposure to nitrogen and carbon dioxide. In addition, oxygen depletion in confined spaces is a particular issue with biomass storage.
A further safety concern, which is well known to areas of industry dealing with biomass storage, but potentially not so well known to new market entrants looking at SAF feedstock, are the hazards associated with carbon monoxide.
For example, Hydrotreated Depolymerised Cellulosic Jet Fuel (HDCJ) is one of a number of innovative pathways which are being explored, in addition to the main SAF technologies, in a bid to diversify SAF production. HDCJ uses lignocellulosic biomass (wood residues, crop waste) broken down through pyrolysis, the chemical decomposition of organic (carbon-based) materials through the application of heat, or hydrothermal liquefaction, a process using heat and pressure, to produce bio-oil.
If you have large scale storage of, for example, crop waste or sawmill waste, significant volumes of this feedstock can create a thermal reaction deep within the mound. This heat can be sufficient to begin inefficient combustion of the feedstock, producing carbon monoxide, an acutely toxic gas.
As these examples illustrate, it is important to understand the specific hazards of each SAF process and respond accordingly with the correct safety technology – particularly gas and flame detection technology. Such systems are vital safety considerations in the production of these fuels.
Power to liquid
There have been advances in the use of hydrogen in aviation in recent years, with some promising results on a small scale. Hydrogen tanks are lighter than those required for HEFA and non-HEFA fuels, and the indications are, significantly, that 100 per cent of hydrogen could be used. There is some way to go before this is a reality – particularly for long haul flights – but it is thought that this form of SAF will be easier to scale.
Clearly, the hazards in relation to hydrogen usage are becoming better known as hydrogen technology advances, and there is work being carried out currently at the University of Aberdeen looking at the transport of hydrogen, a research project which Dräger is supporting by advising on the safety aspect. This will look at a wider transport distribution network but the project’s research into structural integrity when in contact with hydrogen and preventing hydrogen leakage will be essential in hydrogen applications, including SAF.
As is the case with all renewable energy, there is a sense of the unknown when it comes to safety. However, providers like ourselves are very experienced in a range of relevant safety issues, such as gas detection, in a wide range of different scenarios and will be able to use our knowledge to address safety in this sector as it develops.
Ensuring the success of SAF is not only about meeting targets; it’s also about embedding safety from the ground up. We are already working closely with companies developing new SAF technologies, and these partnerships will be essential in bridging the gap between innovation and safety, ensuring the industry continues to grow – safely and sustainably – to 2030 and beyond.
For more information, see: draeger.com/en_seeur/Safety/Clean-Energy-Solutions
Megan Hine is Energy transition safety lead at Draeger Safety UK
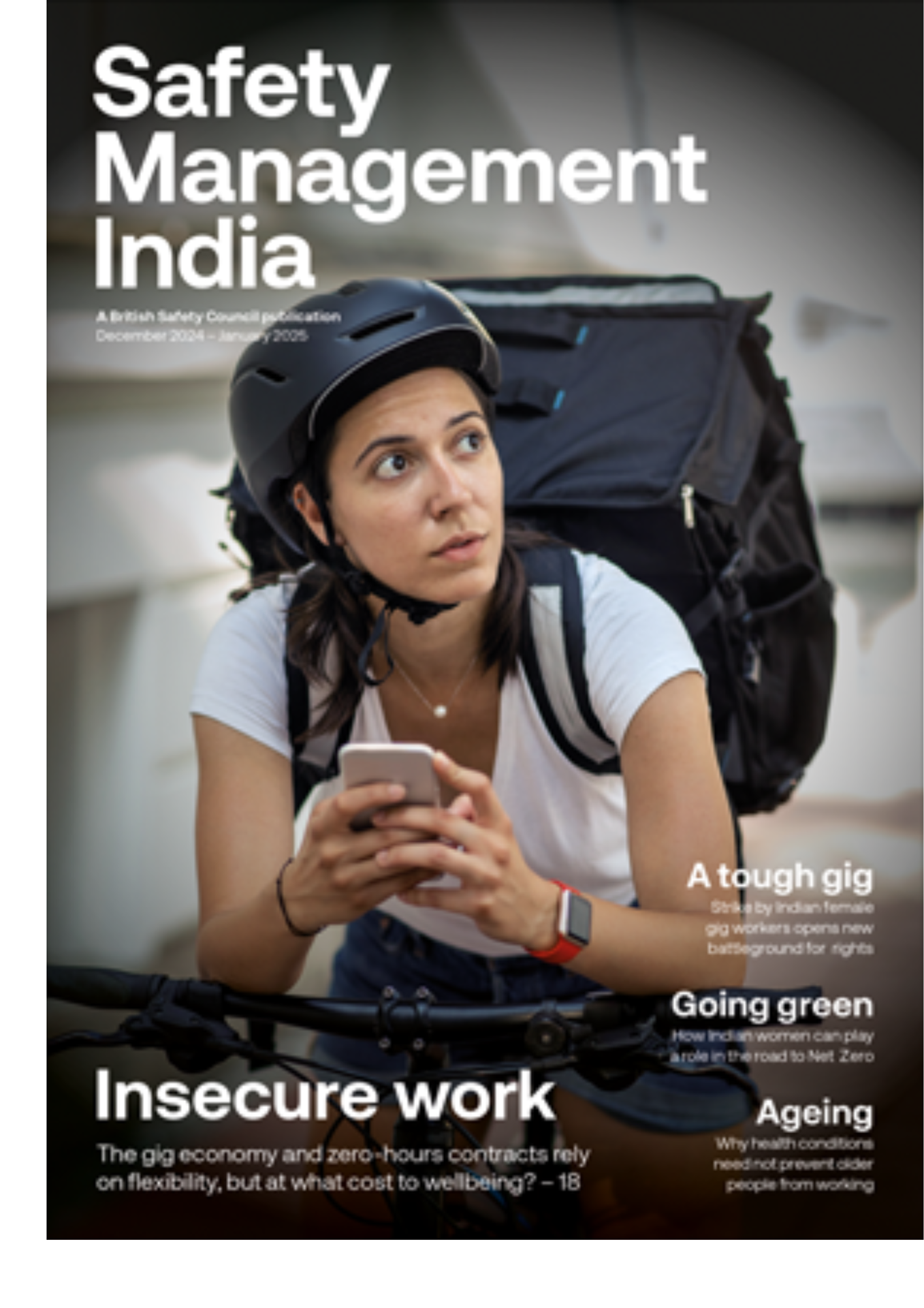
