Process safety incidents at major hazard plants, such as chemical and gas leaks, can have catastrophic consequences for workers, local communities and the environment. However, by carefully assessing the risks and establishing suitable policies, systems and procedures, businesses can keep everyone safe, explains Amresh K. Deshmukh, head of process safety management at British Safety Council.
Features
Process safety management: the importance of getting it right
What is your background and experience in the health and safety field to date?
I began my career as an instrumentation graduate working for a manufacturing company. During this period, I focused on minimising human intervention in operation. The approach was efficiency-driven with a limited focus on reliability.
From 2007, I worked as a plant engineering manager for major chemical manufacturing companies, responsible for the safe, day-to-day running and maintenance of production lines and other risky areas of high hazard chemical manufacturing plants. During this time, I adopted a more granular approach, with the aim of ensuring safety was embedded in every project I was engaged in. This approach helped me to prevent the loss of containment of highly hazardous chemicals at the various chemical manufacturing plants I worked at until 2014.
In 2014, I decided to pursue process safety management as a career. I began working for safety consulting firms, helping high hazard organisations, such as petrochemical refineries and chemical manufacturers, improve their process safety performance. In my various roles over the past 15 years, I have seen high hazard organisations, such as chemical manufacturers and oil and gas companies, following a path of continuous improvement and striving hard to prevent safety incidents that could have an adverse impact on workers, people and the environment.
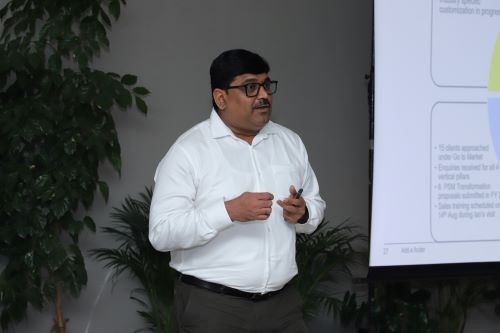
What do you think are the biggest challenges facing those responsible for health and safety at work and the most important skills for health and safety practitioners?
The basic principles and vital importance of health and safety at work are not taught in schools in India (whether at primary, secondary or higher secondary level) and the subject is not covered at university and degree level, unless someone voluntarily chooses it as a topic of interest.
This is a major hurdle as it is essential that everyone at work – including in the process industries, like oil, gas and chemicals – understands how they can play a pivotal role in ensuring safe day-to-day operations and tasks. For employers and safety practitioners seeking to introduce health and safety initiatives and transform organisational safety performance and culture, this lack of workforce understanding of the importance of health and safety can be an impediment.
One of the main – and crucial – responsibilities of environment, health and safety (EHS) practitioners is to establish adequate EHS competence among all workers at all levels across the organisation. To achieve this, EHS professionals need to engage with all stakeholders across the business – from the board room to the shop floor – to clearly set out how the organisation expects everyone at all levels to work safely, prevent accidents and ill health, and contribute to achieving the highest standards of health and safety.
What is process safety management (PSM), and what are its key benefits?
PSM is about effectively controlling and mitigating the risks arising from the storage, production, handling and use of hazardous substances, such as chemicals, gases, vapours and petrochemicals, in workplaces such as chemical, gas and petrochemical manufacturing, processing and distribution plants.
PSM also covers the management of hazardous conditions, such as stored energy and pressure from machinery and production and processing plant – for example, steam and gas. If hazardous substances are suddenly released, or a hazardous condition suddenly gets out of control, this can cause catastrophic incidents, such as explosions, fires and releases of hazardous substances into the air, ground and nearby waterways. These incidents have the potential to simultaneously kill or injure large numbers of people (namely workers and the public), destroy or damage plant and equipment and cause significant damage and contamination to the environment.
For the companies involved, these catastrophic incidents can seriously harm their reputation and result in widespread negative media coverage of the suspected EHS failings.
What are the British Safety Council’s PSM services and how do they help organisations improve PSM?
British Safety Council has worked very closely with the UK’s safety regulator, the Health and Safety Executive (known as HSE), to develop a PSM framework that can adopted by organisations producing, handling and working with highly hazardous chemicals and gases. British Safety Council works very closely with organisations interested in transforming their PSM practice.
To begin with, we perform a PSM assessment to identify any gaps in the implementation of all elements of an effective PSM system for reducing and managing process safety risks. We develop a transformation programme (with appropriate timescales) for the client that includes establishing a culture of participation and engagement at all levels of the business for effectively managing PSM risks.
A PSM programme also helps organisations and their staff learn how to manage all aspects of PSM and helps embed PSM competence throughout all layers and areas of the business. British Safety Council also helps high hazard organisations to develop their own PSM capability, so they can successfully manage process safety risks themselves on an ongoing basis.
How did British Safety Council develop its new PSM services? Did you involve international PSM experts?
Over the past 20 years or more, British Safety Council has helped organisations in Europe to achieve their PSM objectives. For the past five years, British Safety Council's India office has been working directly on the ground in India, using both Indian and international PSM consultants to help Indian businesses implement suitable PSM frameworks to prevent accidents and achieve high safety standards.
British Safety Council works with Indian businesses in high hazard sectors to develop organisation-specific customised PSM transformation plans. The plans help each business to define their PSM objectives; assist them to build the necessary in-house competence to manage PSM risks and British Safety Council works with them every step of the way to meet their PSM objectives.
British Safety Council’s goal is to provide sufficient support until a company’s own EHS team has sufficient competence to independently run the PSM programme and strive for excellence in the management of process safety.
Why should Indian businesses choose the British Safety Council for advice, help and support in managing process safety?
British Safety Council has been at the forefront of delivering cultural and occupational safety and health (OSH) transformation services and support to all types of businesses in India for many years. We are quite well-known in India for conducting Five Star health, safety, wellbeing and environmental management audits, which assesses and benchmark an organisation’s OHS, wellbeing, environmental and sustainability policies, systems and performance against the latest legislation, standards and best practice.
These EHS audits provide assurance of excellent performance in these areas and recommendations for further improvement, where necessary.
British Safety Council is also well-known and respected for our training programmes that have helped a wide range of organisations of all types, sizes and sectors to achieve their OSH and EHS objectives.
We are now focusing on providing PSM support, consultancy, audits and training so organisations in high hazard industries can achieve the highest standards of process safety by implementing a comprehensive PSM transformation programme.
How comprehensive is the level of understanding among companies in India’s process industries, such as oil and gas processing and chemical manufacturing plants, about the potential OSH risks and how serious a process safety incident could be for workers, the public and the environment?
In recent years, there has been quite a number of process safety incidents in India and companies in high hazard industries are increasingly taking note of the significant impact these incidents can have on workers, the local population, the environment and the company’s ability to operate in an efficient manner. Most high hazard sector companies are eager to learn from process safety events at other plants and prevent similar incidents occurring at their sites.
Organisations sometimes miss the key point that ‘hazards don’t care’ and are indifferent to whether or not the business has a programme to prevent or mitigate process safety risks. Hazards arise from weaknesses in an organisation’s technology, safety systems and OSH culture. It is therefore essential that high hazard plants seek to constantly improve their understanding of process safety hazards and take appropriate steps on an ongoing basis to minimise the risk.
The Bhopal gas tragedy at the Union Carbide pesticide production plant in 1984 is a stark reminder of the critical importance of PSM, and India witnessed another serious gas leak at the LG Polymers chemical plant in Vizag in 2020. Although the Vizag tragedy is perhaps not comparable to the Bhopal disaster in terms of fatalities, the two have many chilling similarities – both took place at night, involved a catastrophic release of toxic chemicals and had devastating and fatal consequences for the highly populated communities outside the plants.
December 2024 marks 40 years since the Bhopal disaster, so is PSM now an integral part of the day-to-day management of all major hazard plants in India – from design to operation and final decommissioning? Or does India’s process industry still have a long way to go to improve PSM?
Unfortunately, it is too early to say that full and effective PSM is an integral part of every high hazard business in India. In the recent past, there have been incidents in India that have once again highlighted the impact of catastrophic process safety incidents on society at large.
High hazard organisations need to understand that ‘one accident is one too many’. Awareness of process safety in high hazard industries is certainly increasing. However, some organisations are failing to quantify the amount of effort required to properly identify, analyse and manage process safety risks. As a result, they fail to allocate sufficient time and resources to achieve the desired outcomes from their PSM programme.
It is therefore essential that organisations spend sufficient time and resources identifying and analysing process hazards. The entire PSM programme must be developed using the right framework and must address the specific hazards identified and analysed by a comprehensive risk assessment. A risk-based approach will help an organisation narrow its focus on developing and establishing policies, systems and procedures that will either prevent or mitigate process safety incidents like gas and chemical leaks, fires and explosions.
Do India’s high hazard organisations see safety as an investment or just an expense? Do they realise that a small investment in PSM programmes can prevent significant costs arising from industrial safety disasters, such as compensation for workers and communities, legal fees and financial losses in the market due to loss of business reputation?
As safety practitioners, we need to educate everyone in an organisation – including the directors and managers – about the fact that decisions about process safety can have an irreversible impact on people and the environment. High hazard companies need to ingrain this thinking in their decision-making on ways of managing the risks from highly hazardous and toxic chemicals.
Compensating workers and communities for damages, legal fees and financial losses following process safety incidents can result in significant costs for a business. So, the focus has to shift to prevention and it is essential that businesses take action to prevent incidents, including, if necessary, shutting down areas of a plant until the PSM risks are addressed. A sensible pause in operations will give an organisation time to properly analyse the risks and develop the right PSM solutions.
Developed nations enforce PSM regulations in hazardous industries, but the Ministry of Environment, Forest and Climate Change and the Pollution Control Boards does not consider process safety when issuing environmental clearances allowing certain large industrial activities (such as oil, gas and chemical processing plants), to proceed. Does India need to amend its legislation?
The current set of regulations and various recommendations released by government committees following the Jaipur oil depot fire that killed 12 people and injured over 300 in 2009 and the LG Polymer Vizag incident in 2020 provide adequate inputs to strengthen companies’ PSM programmes. The regulations act as a deterrent for EHS offences by companies as they are useful when there are violations.
As far as PSM is concerned, it is essential that organisations focus on preventing process safety incidents in the first place. When developing and implementing state-of-the-art PSM risk management programmes, organisations also need to pay equal attention to mitigation plans to ensure they are complying with India’s occupational safety and environmental laws.
A number of languages are spoken in India and misunderstanding of verbal instructions and written processes are known factors in causing safety incidents. Also, good health and safety communication is essential at all levels for accident prevention. Do businesses need to consider language barriers and teh adequacy of communication methods when addressing process safety risks?
Possible language barriers and the effectiveness of all safety communications can have a detrimental effect on the management of risks and this needs to be considered and addressed at the beginning of a PSM programme.
Although a company might develop the best PSM policies, procedures and guidelines, if these are not fully understood by everyone – from managers to workers – then the overall implementation will fall short and PSM risks will not be properly managed on a day-to-day basis.
However, as well as language barriers and poor OSH communication methods, it is also essential that everyone at work is willing to participate in dialogue about safety. If everyone is to buy in to good PSM, they must be provided with adequate information on the OSH risks and their role on keeping the plant and its people safe.
Based on your experience as an auditor, advisor and trainer, can you give examples of excellent PSM by Indian companies? Are there examples of Indian businesses excelling at PSM – and how?
For business confidentiality, I won’t name any specific companies, but I have come across many organisations who have a very good understanding of the inherent risks involved with handling and working with highly hazardous chemicals and other substances. For example, some high hazard plants have moved the production and processing of certain products to more suitable locations to reduce the EHS risks both to workers at the site and the local community.
Some businesses have engaged all stakeholders, including the original equipment manufacturers and contractors, while implementing process safety.
When managing process safety, companies have to ‘connect the dots’; they have to foresee and develop a programme of continuous safety improvements to help them ‘guesstimate’ both the likelihood and consequence of incidents at their plants. Over time, the ‘guesstimates’ will begin to narrow and the process safety team will become much more effective at estimating the likelihood of a harmful event, identifying the likely consequences and deciding how to effectively prevent these incident occurring, therefore keeping everyone safe.

