Noise emission data from machinery manufacturers can help purchasers identify the most suitable machine when buying or hiring new equipment, but it’s also essential to maintain the machinery correctly to minimise the noise levels.
Features
Make sure you buy quiet
Employers and duty holders are required under the Provision and Use of Work Equipment Regulations 1998 (PUWER) to provide workers with equipment that meets relevant supply laws. They must also adhere to the Control of Noise at Work Regulations, and the Health and Safety Executive (HSE) offers guidance which sets out an employer’s legal obligations.
Machinery manufacturers are legally required to provide information about the noise emissions from their machinery if it exceeds certain levels. They are also legally required to ensure that it is designed and constructed to reduce noise risks to the lowest level, alongside use of protective measures and information relating to any remaining noise risk.
Photograph: Shutterstock
Purchasers of machinery should therefore expect equipment being sold on the market to reflect technical progress in low-noise design.
To ensure that noise levels are minimised, not only should purchasers take noise into account when selecting machinery, they should also ensure that it is maintained in accordance with manufacturers’ recommendations. Machines deteriorate with age and use, and if they are not maintained appropriately, they are likely to generate more noise because of worn parts, poor lubrication and the vibration of loose panels.
Appropriate maintenance should therefore prevent noise emissions increasing over time and ensure that a machine’s performance does not deteriorate so that it puts employees at risk from increased noise emissions. Likewise, it is vital to have a company policy in place that requires machinery operators to report any unusually high noise levels and which ensures they regularly check that machines are operating properly.
Darren Hugheston-Roberts is head of machinery safety at TÜV SÜD. Photograph: TÜV SÜD
The Supply of Machinery (Safety) Regulations 2008, which is the UK implementation of the European Union’s (EU) Machinery Directive, require manufacturers and suppliers of machinery to comply with the applicable essential health and safety requirements (EHSRs). These are:
- Produce machinery that can be used without risk, including risk from noise
- Alert users to residual risks including risks from noise – for example, when a noise test code produces noise emission values that do not represent noise emissions during intended uses of machines
- Include the information on airborne noise emissions in the sales literature describing the performance characteristics of the machinery
- Provide information in the instructions accompanying the machinery, including instructions on how to reduce risks from noise.
Outdoor use
There are also separate regulations for equipment for use outdoors – the Noise Emission in the Environment by Equipment for Use Outdoors Regulations 2001. This requires that the guaranteed sound power level must be marked on the equipment. The responsible person must also ensure that the machinery has been CE/UKCA marked and has the indication of a guaranteed sound power level. The equipment must also be accompanied by a declaration of conformity. Qualifying Northern Ireland products can be placed on the GB market with the CE or CE+UKNI conformity markings.
A full list of equipment to which the 2001 Regulations apply can be found in its Annex A.
This covers equipment subject to noise limits, such as compaction machines and loaders, as well as equipment subject to noise marking, such as conveyor belts, high pressure flushers and power generators (those with a power consumption above 400 kilowatts, or kW).
For equipment that is subject to noise marking, the manufacturer, or their authorised representative, must subject the equipment to an ‘internal control of production procedure’. This procedure is referred to in Annex D and does not require the involvement of ‘approved bodies’, which are UK-based conformity assessment bodies.
Any equipment that is subject to noise limits must be subject to noise emission limits tests before it can be placed on the market or put into service. This means that the manufacturer, or their authorised representative, must subject equipment to one of the following conformity assessment procedures:
- The internal control of production with assessment of technical documentation and periodical checking procedure referred to in Annex E of the relevant guidance on the 2001 Regulations
- The unit verification procedure referred to in Annex F, or
- The full quality assurance procedure referred to in Annex G.
Any of these three assessments will require the involvement of approved bodies for UKCA and/or CE+UKNI Marking. CE certification assessments carried out by non-UK Notified Bodies can currently be accepted and the UK government had communicated an intention to accept CE marking beyond 31 December 2024; however, at the moment this is still an ‘intention’ with no legislation in place. There are some conformity assessments bodies within the UK that can perform both UKCA and CE conformity assessments.
Anyone found not to be complying with the Regulations may be liable to a penalty, which includes a fine or a prison sentence of up to three months (or both) for the most serious offences.
Correct information
HSE advises that machinery owners check with their manufacturer and/or supplier to ensure that the noise information they have made available is a reliable guide for the intended use of the equipment. A manufacturer should therefore state emission sound pressure levels that are representative of the noisiest operation in typical use of a machine. This means that they may provide noise emissions for more than one operating condition for some classes of machine.
Photograph: Shutterstock
Even though BS EN ISO 12001 states that noise emission data should represent the noisiest operation in ‘typical use’ of the machine under test, it is worth noting that data may not always be supplied for the noisiest operation. If the purchaser has a specific use in mind for the machine, they can also ask the manufacturer to provide relevant noise data, but this is not a legal requirement.
Ultimately, the manufacturer’s noise emission data in the instruction manual should enable the purchaser to compare similar machines and identify the most suitable machine when buying or hiring new machinery.
Darren Hugheston-Roberts is head of machinery safety at TÜV SÜD.
TÜV SÜD is one of the world’s leading experts in product testing and certification. For more information see: tuvsud.com
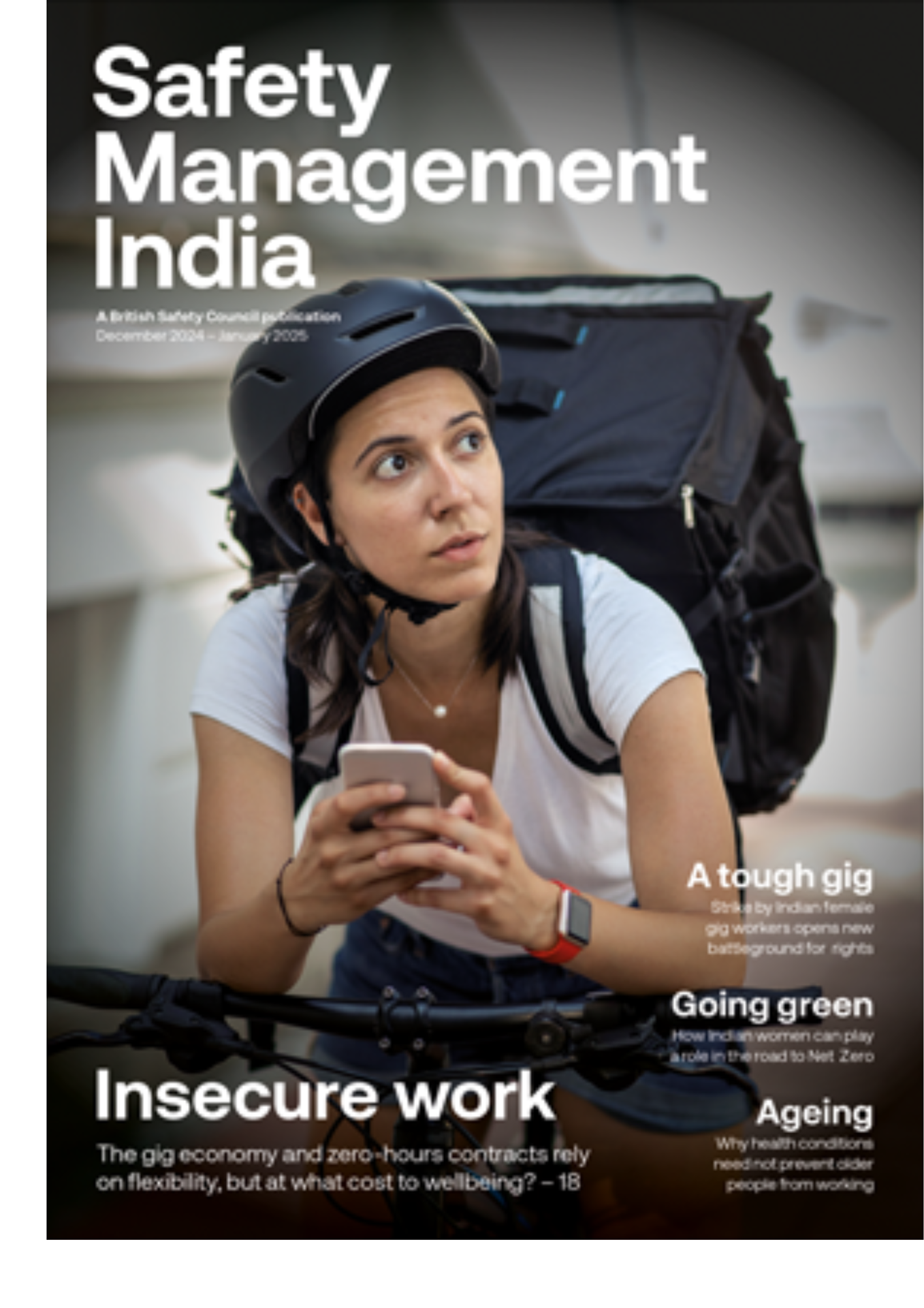

FEATURES
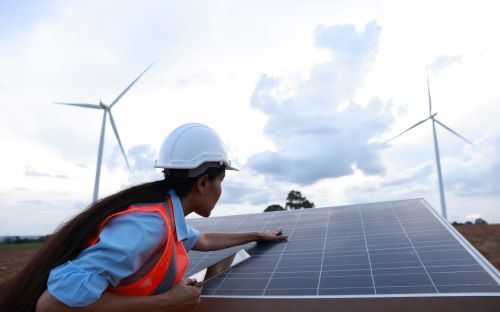
India’s path to net zero: a work in progress
By Orchie Bandyopadhyay on 08 April 2025
India is implementing a variety of clean energy measures to hit its target of net zero greenhouse gas emissions by 2070, including plans to rapidly scale up the generation of nuclear power. However, climate experts say significant finance will be required from developed countries to phase out coal power, accelerate renewables deployment and expand the national electricity grid.
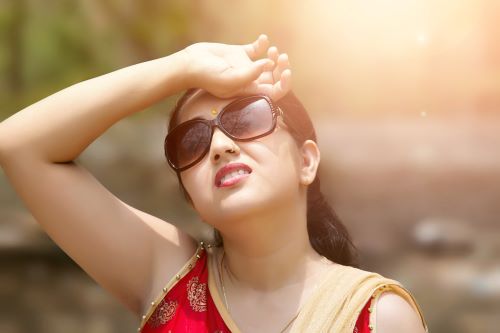
Too hot to handle: early arrival of heatwaves in India sparks calls for action to protect workers and the public
By Orchie Bandyopadhyay on 08 April 2025
Temperatures in India in February 2025 were the hottest since records began over a century ago, prompting warnings the country needs to urgently step up efforts to protect both workers and the general population from the health risks posed by extreme heat and humidity.