A behind the scenes tour of the Royal Opera House, the iconic building in London’s Covent Garden, was organised by the Women in Health and Safety network. For Safety Management, it was a chance to see what goes into making those magical moments on stage.
Features
Safety behind the spectacle: backstage at the Royal Opera House
“It’s not an opera house, it’s a castle, and it has turrets and so you can’t get from one turret to another, you have to go down across the drawbridge.” Alexandra Lucas, health and safety manager at the Royal Opera House (ROH), is describing the venue’s unusual layout, meaning we need to take lifts to traverse it.
It’s an imaginative yet fitting description for a building where wonder and make-believe are everyday business. And Alex’s tour is packed with amazing anecdotes about what goes for normal life here – everything from squirrels doing pliés in the side of stage, to designing an exploding chocolate pot.
The Grade I listed auditorium seats 2,256 people. Photograph: Sim Canetty-Clarke
Artists and directors are forever coming up with spectacular ideas, all of which need the careful eye and guidance of the safety professional, but it’s very rare that the team say no. “We would always want to be more like ‘how can we achieve this’,” she explains of safety’s role in supporting (not interfering in) the artistic process.
On the day of our visit, at the end of July, there are no dancing squirrels to see, as summer is an unusually quiet time. This evening, Carlos Acosta will perform a retrospective of his work, but for three weeks during the summer there are no opera or ballet shows on stage.
On normal days, the ROH juggles three or four shows a week on stage – plus two in the rehearsal rooms. Operas are often limited to runs of only six performances. The turnaround in the building is phenomenal, and Alex comments that ROH is probably the busiest repertoire house in the world.
A ’dynamic’ environment
Our tour starts in the Grade I listed auditorium which seats 2,256 people in a horseshoe design. The red and gold interior is luxurious, like the inside of a jewellery box. One of the first surprising facts is that the ROH has twice burnt down in its history. The fires were in 1808 and 1856, and today, fire is still taken seriously as a risk.
A full-time fire manager supports the estate, while security fire wardens stand by when pyrotechnics or fire effects are used on stage. Beyond this, risks are varied. The venue employs more than 1,000 full-time staff: wigmakers, costumiers, a full-time orchestra and production staff among them.
Photograph: Sim Canetty-Clarke
It all sounds quite jolly, but that’s not the whole story of being a premier opera and ballet venue: Alex acknowledges the risk level is not “the same as construction” but while not building a huge residential block or a factory, “stage staff work at height and in the dark a lot and the theatre provides a very dynamic environment.”
Making performers feel safe
Additionally, there are the visiting opera stars, all interacting with the spaces and massive scenery. Ensuring their safety brings unique challenges, explains Alex. The health and safety team has talked about the needs of their visiting performers, everything from how to induct them to how much supervision they might need. “That’s been really interesting,” she says.
Actors and singers can have precarious existences and may bring these anxieties to a job. Performers are often freelance and the challenge is to create an environment where they feel secure enough to speak up about safety as the production develops. Alex describes the need to make people feel confident about raising any safety concerns.
Backstage at The Nutcracker. Photograph: Andrej Uspenski
Logistics
Opera and ballet isn’t just about the stars, but the whole package including making and transporting the stunning scenery. The ROH has two rehearsal spaces measuring about the same size as the main stage. A lone violinist is today practising in one, but on normal days, says Alex, the technical team can drive in a full-sized set and rehearse on it here, reducing the need for stage time.
Sets are built at production workshops in Purfleet in Essex. Once delivered to the ROH, the build team will unload these flatpacked creations, ready to be re-assembled to their rightful glory and become giant trees, a ruined city, or a golden door. Some operas can take up to 16 huge pallets or more for just one show, so it’s a big operation. A large warehouse in Wales stores all the sets once they’re finished with.
It means that manual handling and offloading are also risks. The health and safety team visit both sites to keep on top of safety with the hope that the more they go, the more the staff will want to talk and ask advice.
Sets are built at production workshops in Purfleet in Essex. Once delivered to the ROH, the build team will unload them.
During the show these very same props and scenery will be hoisted, moved, or flown onto the stage, powered by a combination of people and a precisely timed automated system.
The deputy stage manager controls everything, calling out verbal cues from the master script. The technical team then kick into action, pressing buttons to lift curtains or physically place props. “No one is allowed to do anything until the stage management team says – it’s all operated a bit like air traffic control,” says Alex.
Flying down on a Stannah stairlift
Every year, all machinery and stage gear must be checked as part of Lifting Operations and Lifting Equipment Regulations (LOLER). That sounds normal enough, but when you consider some of the machinery has to fly people across the stage at up to 14 metres high, it is essential. In the past, they’ve achieved such feats as making Anna Nicole Smith’s 86-year-old husband fly down on a Stannah-style stairlift (in an opera of the troubled model’s life).
Aerialists performing in Dvorák’s opera, Rusalka, looked like they were swimming in water. Beautiful stuff, but highly technical. If any performer is flying in a show, a thorough examination [of the equipment] is carried out again even if the inspection was already done two months ago. An external company is brought in to help. As Alex says, it’s something you don’t want to get wrong.
Sound check
There are also less obvious risks that come with opera staging. An important one is found in the orchestra pit. In 2018, a viola player won a High Court judgment against the Royal Opera House for acoustic shock.
In the first case of its kind, he argued that the incident was partly due to where he was sitting – in front of the brass section – in a rehearsal of Wagner’s powerful Die Walküre (The Valkyrie) opera.
The ROH has always taken steps to look after the musicians’ hearing, with a full programme of hearing health support; but after the case was lost (all information on the case is publicly available) they had to review everything and see what more could be done. “We had a programme already, but the court case has meant we’ve just looked at everything,” says Alex.
This might mean not putting certain shows next to each other in the programme if they are both very loud to reduce noise exposure and help the orchestra pace themselves with a more reasonable weekly exposure.
The orchestra pit has also been extended by taking out some seating on both sides of the auditorium and for most of the repertoire, ROH no longer sells those seats to create a bigger pit and have more space for the different sections, so strings can be further away from brass and percussion can have more space.
The ROH is a huge operation. Yet, the tour has shown just how much a part of the whole production health and safety is, rather than just an adjunct. One thing that has helped, says Alex, is simply where she sits.
Six years ago, she moved where she sat from operations to technical and production. “Initially, it was ‘why are you here?’ that suspicion of health and safety people. In six years we’ve transformed that, [they can see] we’re not trying to trip people up, or make life more difficult, we’re here to enable you and give you more support and advice – that’s the dream! I think the relationship has completely transformed and it’s gone from taking up desk space to ‘Alex, I want you to look at this’….. which has been really helpful.” It sounds like Alex has the dream job in a dream venue.
Royal Opera House: www.roh.org.uk
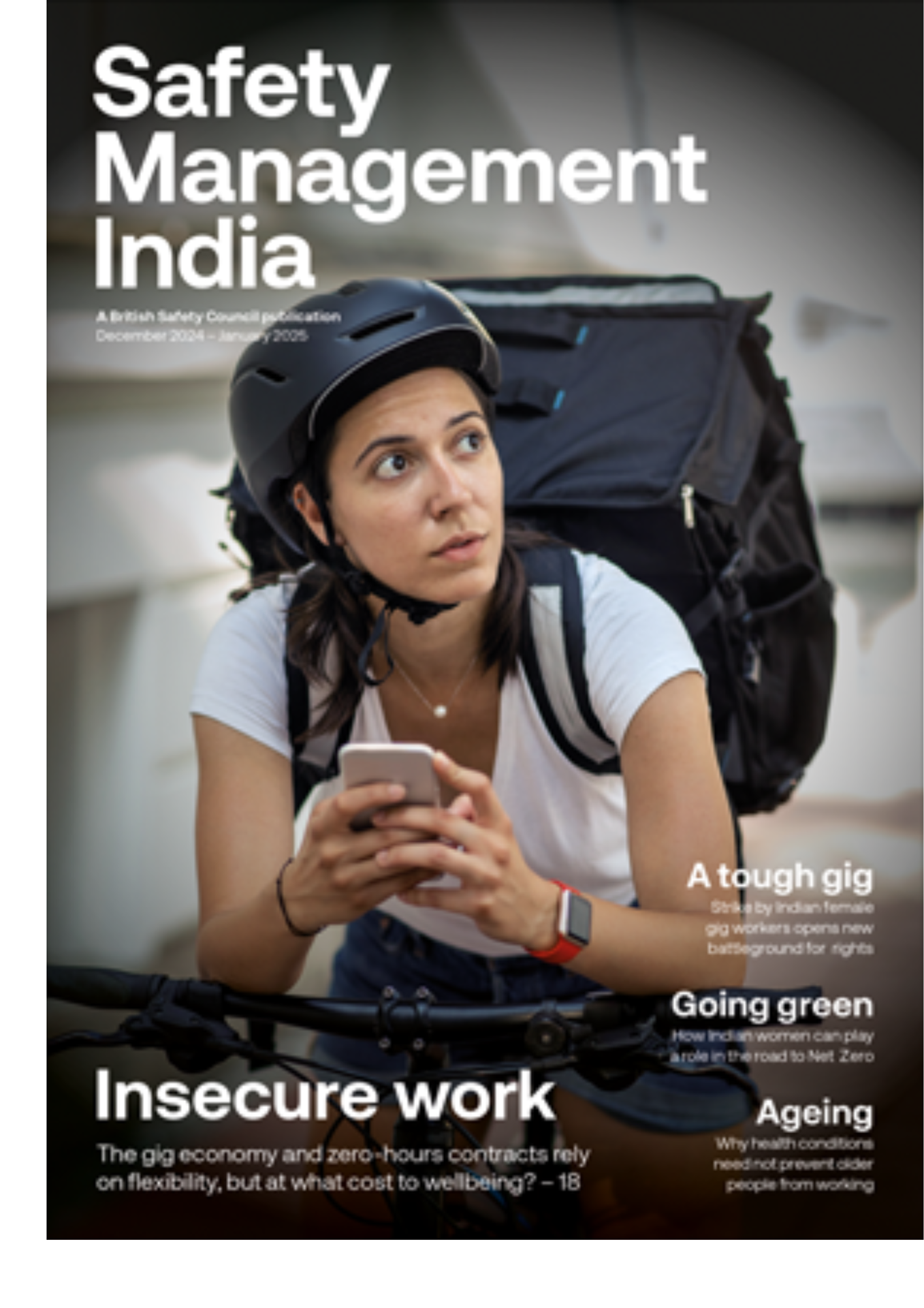
