Musculoskeletal disorders are a major cause of work-related ill health, so manufacturers of materials handling equipment are increasingly adopting ergonomic principles and design features to reduce the risk of injury when operating forklifts and similar machines.
Features
Preventing MSDs: how handling equipment design is helping
Although accidents and fatalities tend to make the headlines whenever forklift safety is discussed, I’m pleased to see the focus is shifting to the profound impact of musculoskeletal disorders (MSDs). Read on and I’ll share some examples of recent innovations designed to help alleviate the problem.
Of course, concern about the numbers of workers killed or injured each year in accidents involving materials handling equipment is legitimate. After all, the numbers continue to be unacceptably high and every death or serious injury – usually to someone on foot, working alongside a forklift – forever changes the lives of all involved, including victims, their families, colleagues and employers.
But the same is true for those affected by MSDs.
Readers of Safety Management will be familiar with figures published by HSE (2021/22) revealing that 477,000 workers were currently suffering from this condition.
As a safety professional you may also employ the HSE’s excellent Back Injury Risks in Driving (BIRD) tool which outlines five steps designed to help employers evaluate workplace safety and identify ways of addressing any shortcomings.
In a recent podcast, the creator of BIRD, Matt Birtles, who is principal ergonomist at HSE, emphasised that of the five aspects covered by the process, reducing harmful factors is key, and said: “That is where the biggest difference can be made.”
Manufacturers of materials handling equipment are increasingly adopting ergonomic principles and design features to reduce the risk of injury when operating forklifts and similar machines. Photograph: Red Diamond Distribution
Providing the appropriate equipment
It’s heartening to see the levels of investment that manufacturers of materials handling equipment are clearly assigning to researching the causes of MSDs (and other ailments caused by stress, vibration and poor ergonomics), and in developing not only innovative machines but also transformative software.
The results have, for some time, been highly visible in the game-changing improvements to seats. Modern suspension seats catering to an ever-greater range in the size of operators allows each of them to achieve their optimum driving positions. Importantly, they also allow operators, at the start of a shift, to adjust the cushioning to match their weight. This is important in minimising vibration and jolts, especially since electric trucks have no suspensions systems, unlike their engine-powered counterparts.
This brings us onto some of the developments which may be new to anyone who hasn’t replaced their handling equipment in recent years. Talking to a senior designer at Mitsubishi Forklift Trucks I asked about the overarching design philosophy behind the range and was told the focus is on creating trucks that are smooth and effortless to operate and, crucially, utterly predictable. Proof that their efforts are successful comes from the ever-expanding cluster of Archies and Red Dot Design Awards for ergonomics.
Ergonomic features worth considering
Here, then, are a few examples of ergonomic features you may want to look for when considering your next forklift or warehouse truck:
360-degree steering is still under patent but promises to become widespread because it ticks several boxes. The first is that it greatly reduces the number of whole-body manoeuvres involved when changing truck direction. The technology enables the operator to switch direction effortlessly, without pausing, and without the necessity for a laborious and time-consuming three-point turn.
Not only does that reduce strain on the operator but, by greatly reducing centrifugal forces, it reduces the risk of loads being thrown from the forks. As an added bonus, because of its smooth, continuous motion, precious seconds are shaved off every manoeuvre – invaluable in fast-paced picking manoeuvres – increasing productivity whilst reducing effort.
Adaptive lift control (ALC) is another new development. Its function is to automatically control lift/lower, tilt and side-shift speeds regardless of the weight of the load.
When handling heavy loads, conventional trucks are set up to force the maximum power through the motor to deliver the necessary hydraulic performance. That’s fine when the truck is fully laden but that power is excessive when there is no load, resulting in fast mast/fork movements.
Sensing the weight of the load (or lack of it) ALC automatically delivers the appropriate power, meaning the speed remains constant and predictable at all times. No jolts, no surprises.
Another product of increasingly sophisticated software is the use of intuitive drive systems. Already a feature on top-end cars, these enable the truck to learn how each operator prefers to work… and adjust its performance parameters accordingly.
It means that, without changing the truck set-up at the start of every shift to accommodate different styles and capabilities, the truck makes operations entirely predictable for any driver, whether they be a novice, or a confident operator, working in a heavy-duty environment, or one where delicate loads need careful handling.
Until now, each operator was required to accept a generic, one-size-fits-all set up and endure what was frequently a frustrating or stressful shift compensating for unexpectedly aggressive acceleration and turns – with all the compensatory actions putting unnecessary strain on limbs and spine.
Passive sway control is designed to reduce vibration and the consequential discomfort and potentially frustrating delays. It quickly and smoothly overcomes the swaying motion generated when a truck stops with the load raised. Ingeniously, the brakes on the truck are automatically released to allow 5cm of forward and backward travel to gently and rapidly absorb the energy and cease the unpleasant mast movement.
Adjustable armrests, mini steering wheels and fingertip controls have transformed the cabins of counterbalance trucks along with a wide variety of warehouse trucks. Fly-by-wire technology developed from the aerospace industry make operations smooth and precise to reduce strain, with smart software ensuring controls have the necessary resistance to mimic the progressive ‘feel’ of hydraulic levers.
Pedestrian-operated warehouse trucks have not been neglected. Dampened platforms significantly reduce vibrations with one manufacturer now boasting a “triple-suspension floating floor” on its low-level order pickers. Great attention has also been paid to entry/exit in order to make shifts less tiring and to eliminate trip hazards. Controls are better positioned to save operator stretching.
Changing inappropriate processes
In the case of Mitsubishi Forklift Trucks this has involved campaigning to replace hand pallet trucks with power pallet trucks because of the dangers to worker health they pose, especially in applications involving heavy loads or frequent use.
According to the HSE, more than one third of all injuries requiring at least three days off work are caused by manual handling (lifting, lowering, pushing, pulling or carrying). Most of these injuries are strains to arms, hands, fingers and back (which accounts for 47 per cent of injuries), along with sprains to the wrists, thumbs and ankles.
It’s heartening to see the levels of investment that manufacturers of materials handling equipment are clearly assigning to researching the causes of MSDs. Photograph: Red Diamond Distribution
In practice it means that if an employee is moving loads frequently it is the cumulative strain that causes the problem. With heavy loads, it’s the effort involved in starting and stopping – as well as keeping it in motion – that are the key issues.
The official guideline figure for starting or stopping a load is about 20kg for men (typically the maximum baggage allowance at an airport check-in) or 15kg for women. The acceptable figure for keeping a load in motion is 10kg for men and about 7kg for women.
Independent researchers working on our behalf tested 17 different makes of hand pallet trucks in order to obtain accurate average moving loads of 500kg and 2000kg.
The results were conclusive – and shocking.
Starting a 500kg load from stationary took, on average, requires an effort of 23.3kg. However, increasing the load to 2,000kg (two tonne) and the force required was 49.6kg – massively more than the official guidelines.
Raising a 2,000kg load on a pallet truck was also very demanding: on average taking a force of 35.1 kg (again much higher than the guideline). Even keeping a two tonne load in motion – at 30.7kg – exceeded the guidelines by a wholly unacceptable 53.3 per cent.
In summary, my advice would be, unless you can reduce the size of each load to 500kg or less – whilst also minimising the number of operations – the only realistic (and legal) option is to mechanise the handling process by switching from a hand pallet truck to a battery electric power pallet model.
Putting processes in place
In 2021/22 an estimated 7.3 million working days were lost in the UK due to work-related musculoskeletal disorders – a figure which shows little sign of reducing anytime soon.
Employers can play an active role in effecting change in their own workplaces, though, by taking advantage of HSE resources such as its MSD Online Assessment Tool to understand, interpret, categorise and communicate the level of risk and its award-winning Safety Climate Tool, which assesses the attitudes of individuals within an organisation towards health and safety issues.
For more information see: mitsubishi-forklift.co.uk
Ben Haseley is Managing Director at Red Diamond Distribution
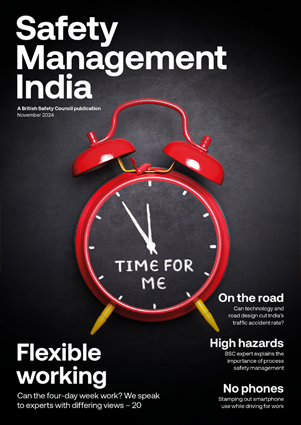

FEATURES
Why changes to recycling legislation in England are an opportunity, not a burden
By on 12 November 2024
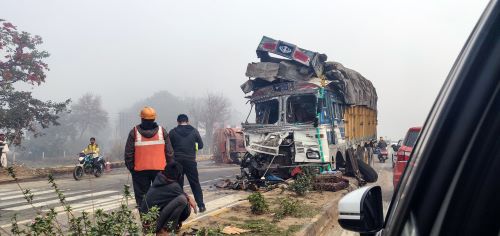
Road safety in India: could better road safety, vehicle technology and enforcement make driving for work safer?
By Orchie Bandyopadhyay on 10 November 2024
India has a poor road safety record, and research shows that commercial vehicles are a major contributor to the problem, with trucks estimated to be the single largest vehicle type involved in impacts leading to fatalities. We look at solutions that could make driving for work and the roads in general safer – from in-vehicle technology that warns truck drivers about unsafe behaviour to improving the design features of major highways.