Palletised freight distribution leader Palletline strives to ensure the highest standards of safety in both its own operations and within the haulage companies that operate as members of the Palletline network across the UK and Ireland.
Features
Palletline: how we minimise risks on the road and in our depots
According to Health and Safety Executive (HSE) figures, 1.8 million working people suffer from a work-related illness and a staggering 36.8 million working days are lost due to work-related illness and injury at an estimated cost of £18.8 billion.
It is therefore vital that businesses and organisations implement measures to build health and safety into their management ethos.
Palletline Ltd, the UK’s leading palletised freight distribution network, is wholly member-owned. It operates a unique multi-hub model, through which members collect pallets of freight from local customers and exchange them at one of its five regional hubs. Established in 1992, Palletline’s collection and delivery services are available throughout the UK and Ireland via its network of 97-member depot locations all covering specific postcodes.
Over 85 per cent of Palletline members are either ISO 45001 accredited themselves or score 100 per cent on our own internal 45001-led audit process. Photograph: Palletline
The company has overcome the significant challenges posed by standardising high safety standards across its member network to create a culture where safety is seen as an absolute priority while also working as a driver for efficiency.
Onboarding
Palletline’s members are shareholder owners of the pallet network, and it is the only pallet network that is 100 per cent owned by its members. Every member signs up to the Palletline Charter, which covers a wide range of operational and commercial rules and requirements for a haulage company to operate as a Palletline member.
A large section of the charter covers health and safety, and the network’s reputation for occupational health and safety (OSH) is a key differentiator for Palletline and in most cases is a significant attraction for prospective members that share the same OSH ethos as Palletline.
All member companies undergo an individual health and safety audit every year to help them benefit from Palletline’s safety success.
These audits follow the ISO 45001 standards and include audits of all OSH processes in place at the member site, including, for example, a review of the company’s OSH policy, management structure, accident reporting systems, OSH posters, vehicle and transport records, PAT testing records, employee handbooks, safety records, risk assessments, training records, fire and emergency procedures, and environmental issues.
The audits ensure each member is fit to be part of the Palletline network and on the rare occasion that a member may fall below Palletline’s standards, Palletline will produce a detailed action plan with agreed time frames for remedial action to take place and will then require written confirmation, appropriately evidenced by the member, that the action plan has been completed.
Over 85 per cent of Palletline members are either ISO 45001 accredited themselves or score 100 per cent on our own internal 45001-led audit process. The remaining 15 per cent all operate above legal requirements.
New members receive their OSH induction within three months of joining the network and particular care is taken to ensure that new employees are aware of the health and safety consequences of their work activities, behaviour, and the benefits of improved personal performance.
While full training is provided, care is always taken to ensure that temporary employees are always supervised by a suitably experienced staff member.
Employing expertise and workforce participation
Palletline encourages employees to take an interest in and responsibility for occupational health and safety matters.
This can be achieved through regular health and safety committee meetings attended by all levels of staff, including appointed shop floor operators who speak on behalf of their collective shifts and then provide feedback to colleagues after each meeting.
Workforce participation has always been key to Palletline’s successful health and safety policy and over the past 17 years, the company has been involving its employees; encouraging them to make suggestions the majority of which have been implemented over the years, where appropriate.
It is a policy which encourages ownership and instils a culture across the business that OSH is everyone’s responsibility. Therefore, all employees take an active role in keeping each other safe, flagging up issues or near misses, including suggesting topics for communication with teams, such as best practices around trailer loading to ensure trailer curtains and poles remain in the best condition, suggestions for improved driver facilities, reporting any disrepair or wear and tear of flooring, equipment, facilities, and keeping the site clean and tidy.
Additionally, ‘toolbox talks’ are held across the organisation and cover all aspects of the operation – but focus closely on safety, ensuring that best practice continues to be top of mind for operatives.
Ken Bell: "Workforce participation has always been key to Palletline’s successful health and safety policy and over the past 17 years." Photograph: Palletline
Examples of health and safety topics covered include mental health, stress, trailer safety, load restraints, seatbelts, staying safe in the heat, opening trailer curtains, and the importance of pre-use checks.
Scheduled for both day and night shifts, the toolbox talks ensure that each member of staff is aware of current issues, all new work instructions and risk assessments, and performance and accident statistics.
One safety measure that needed communicating to staff was the full de-pedestrianisation of the depot.
If lift truck operatives need to dismount their lift trucks, they use a technique called defensive parking. In essence, they park their lift truck defensively (blocking the one-way system) and use the truck as a physical barrier.
This process was extensively tested before it was launched and from the testing, it was established that the lift truck offers better protection than Armco barriers when struck by a lift truck.
As a result, Palletline has had no instances of people being struck by lift trucks in more than 10 years.
The risk assessment process is stringent and includes identifying the risk or hazard and establishing control measures for each task.
Palletline uses risk assessments as effective working tools, performing a systematic examination of each task to identify potential hazards.
The operational team is closely involved with each initiative, completing the task with the responsible operatives and identifying the safest procedures.
Once this has been completed, an Operational Process Control Sheet is created to communicate the findings of the risk assessment. This document identifies the correct way to complete each task and shows images of the correct process being completed.
Investigation and benchmarking
Rigorous procedures for the investigation of all accidents and incidents are in place which has driven year-on-year reductions in accident levels.
Decision-makers need to understand the cause of all accidents and incidents so that they can be confident that any underlying issues are tackled and the likelihood of repeat incidents is reduced.
Palletline is also a proud and active member of the Association of Pallet Network’s (APN) Health and Safety Committee.
As the health and safety manager, I have been the Committee Secretary since 2011, taking a leading role in the forum by painstakingly collating detailed statistics and identifying sector-wide guidance and improvement plans.
This involvement and leadership ensure that Palletline can compare and contrast health and safety approaches across the industry, such as procedures surrounding load restraints and tail lift safety.
Communication and monitoring
Sustained reductions in accidents and incidents achieved over the past seven years demonstrate the effectiveness of the policies that are in place.
Through the APN health and safety meetings, Palletline has been able to compare its accident rates to those throughout the industry and the company is proud to say they are significantly lower than the average.
Targets and measures have been set for every aspect of health and safety within the business. These include the setting of objectives at periodic management review meetings, improvement actions following hazard assessments, and corrective actions following audits or complaints.
For example, the company now operates a monitored 10mph speed limit on-site and all lift trucks are mechanically limited to 10mph. As well as constant monitoring by managers on the floor, vehicle speed is tracked via an on-site speed gun. Speeding drivers are stopped, advised of their problematic behaviour, reminded of the speed limit and issued with a non-conformance. The driver depot company is also informed and provided with all the gathered evidence.
When failures to comply with requirements are identified proactively or following a failure (including an accident, near-miss, ill health or property damage incident), they are formally recorded and investigated.
Investigation
An accident investigation handbook is provided to each of Palletline’s managers who are responsible for investigating any type of accident or incident, together with an accident investigation report template to ensure the data collected is accurate and complete.
Palletline’s managers are trained in RoSPA accident investigation techniques and follow the RoSPA methodology, including how to gather evidence in a timely fashion, and the importance of separating witnesses to ensure independent statements.
Managers are trained to undertake accident investigations immediately, to not only tackle the issue at hand but prevent similar incidents from occurring in the future. In a fast-paced warehouse operation, such as Palletline, robust investigation and documentation are vital to ensuring operational best practice continues to evolve.
Managers are also looking at whether the Operational Process Sheets have been followed correctly. Health and safety is not a static initiative, it requires continuous review, adaptation and evolution of the OSH processes to ensure a business continues to keep its employees and the general public safe.
Examples of Operational Process Sheets that continually evolve include visiting drivers, loading and unloading, the opening and closing of curtains, trailer safety, and operating an FLT.
The Quality, Health and Safety and Environmental Manager conducts a formal investigation into each reported accident or near miss and any issues identified are raised using a Corrective Action Request (CAR), which is included in the Monthly Board Report.
Every member of staff is aware of the seriousness of any safety breach, a statement backed by a low accident level in an environment where 250 fully-loaded Palletline member vehicles visit the main hub in Birmingham each day - a testament to the dedication and conformance of staff.
The Palletline QC Department also checks every vehicle that arrives and departs the site to assess load security and check for unsuitable/banned freight, and incorrect loading.
If issues are noted, such as poor loading, insufficient load security, or damaged freight, then a report is compiled and an incident is raised. This is then issued to the driver, and the depot concerned and a follow-up investigation is then completed by the Palletline health and safety team.
Reaping the benefits
Palletline believes that this level of involvement and participation across the operation have been major contributing factors enabling a consistent annual reduction in accidents and incidents.
This greater level of awareness has created a mindset where all accidents are reported because individuals understand the importance of reporting, to avoid recurrence and to identify trends for their benefit.
This total change in business culture has enabled Palletline to keep safety at the forefront of the organisation whilst enhancing efficiency and productivity.
Although our systems are designed to take precedence over commercial and operational issues, experience has proved that by raising the bar to set the highest standards of occupational health and safety, organisations can also enjoy significant commercial benefits.
Ken Bell holds the NEBOSH (National Examining Board for Occupational Safety and Health) General Certificate and is a qualified lead auditor for both ISO 45001 and ISO 9001.
For more information see: palletline.co.uk
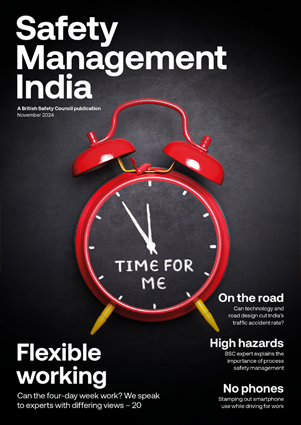

FEATURES
Why changes to recycling legislation in England are an opportunity, not a burden
By on 12 November 2024
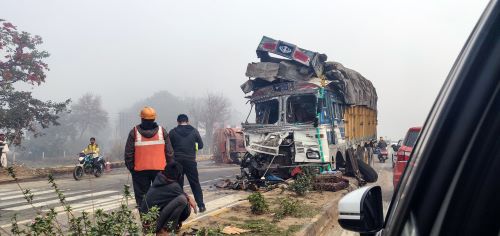
Road safety in India: could better road safety, vehicle technology and enforcement make driving for work safer?
By Orchie Bandyopadhyay on 10 November 2024
India has a poor road safety record, and research shows that commercial vehicles are a major contributor to the problem, with trucks estimated to be the single largest vehicle type involved in impacts leading to fatalities. We look at solutions that could make driving for work and the roads in general safer – from in-vehicle technology that warns truck drivers about unsafe behaviour to improving the design features of major highways.