AI technology is now being deployed to immediately warn mobile plant operators on construction sites of the presence of pedestrians, therefore adding a new layer to transport safety.
Features
Can AI eliminate workplace collisions?
In the past 20 years, we have seen marked improvements in the UK’s workplace safety. In 2002/03 there were 227 fatal injuries to workers; last year the figure was 135, according to HSE. Within construction, my own industry, the figures for fatal injuries fell from 71 to 45.
However, as we all know, any death or life-changing workplace accident is one too many. Of several stubborn underlying trends that need addressing, my particular focus is workplace collisions. People being struck by a moving vehicle remains one of the top three fatal risks, accounting for 15 per cent of the total number of deaths. I believe that these deaths are all avoidable – and AI offers the solution.
Collisions in context
In simple terms, a collision happens when one object comes violently into contact with another. Energy is transferred between the two – the larger an object is and the faster it is moving, the greater the energy transferred and the greater the impact of the collision. On a construction site – where you can find an excavator weighing 40 tonnes moving around in a confined, busy space – the risk is immense.
The AI system is installed onto plant or machinery and detects the human form, acting as a third eye for the operator. Photograph: Safety Shield Global
My personal mission to stop plant hitting people began back in 2013, when a friend was fatally crushed by an excavator on a construction site. Despite physical barriers, use of PPE, clarity around drivers’ and site workers’ responsibilities, and measures for safe vehicle circulation, workers remained vulnerable to the risk of people-plant interface (PPI). I decided to try to harness new technology to tackle the problem.
Having set up a research and development team with a colleague, we drew inspiration from an electric garage door opener for our initial innovation. The UK’s first RFID (radio-frequency identification) safety system used electromagnetic fields to identify and track tags attached to objects. We implemented this successfully at my own construction company, installing a sensor to plant and fitting tags to workers’ hard hats. If someone got too close to a piece of moving machinery, the tag would vibrate and an alarm would go off to warn the plant operator.
Although the sensor and tag system is still used in the construction industry today, it clearly has limitations when people don’t comply with wearing tags. It was a good starting point, but was never going to eliminate workplace collisions. Seeing the success of AI for collision avoidance in the automotive industry, we decided to move on to exploring the possibility of adapting this technology for PPI.
AI for collision avoidance
The outcome – the most advanced application of AI to workplace collision avoidance yet – is made up of three key elements:
- The AI core unit – the brain of the system, containing the central processing unit that all components connect to
- HD cameras – waterproof, dust-proof and shock-resistant, with a recognition distance of 0.5m to 50m
- The operator interface – a simple, user-friendly warning system in the cab that provides visual and audible alerts for the operator.
The AI system is installed onto plant or machinery and detects the human form, acting as a third eye for the operator. Different visual and audible alerts go off in the cab if a person enters the machine’s amber (outer) zone or red (inner) zone, at which point a collision is imminent.
Jonathan Guest: "It took 10 years – and the support of transport authorities, research institutes, international construction companies and OEMs – to develop the AI platform."
Training the model to detect the human form in a construction environment proved a complex, lengthy challenge. Construction sites include varying terrain, multiple signs, machines and materials – all of which initially confused the system into sending alerts for objects rather than people. When it came to the people themselves, the AI technology needed to be able to recognise workers who were crouching down, walking past a container, popping out of a manhole, wearing hi-vis clothing…
It took 10 years – and the support of transport authorities, research institutes, international construction companies and OEMs – to develop the AI platform. Its reliability has been confirmed through six ISO certifications and accuracy measures of 99.6 per cent by independent testing bodies.
The AI collision avoidance system has already been fitted to over 5,000 items of plant in the UK – with zero people plant interface accidents.
Behavioural change
With the support of a cloud-based monitoring system, the technology isn’t just preventing collisions happening in the moment – it is helping to reduce the risk long term by changing behaviour.
Whenever an alert is triggered by the AI system on site, information is sent to a data centre. The centre keeps a record of alerts, video footage of incidents, driver behaviour and vehicle location. It also has a facility for live streaming, so any of the cameras can be viewed in real time through an online portal.
Analysing the data is proving invaluable in identifying trends, spotting specific issues, and predicting likely incidents on a site. In some cases, video footage has prompted changes to the site layout to improve safety. In others, data about incidents has informed on-site toolbox talks (short health and safety presentations) to tackle a specific issue through awareness raising and training.
The statistical impact is clear, with an average 65 per cent reduction in red zone incursions around plant fitted with the AI collision avoidance system in 2022/23.
The final element: autonomous braking
With AI already making its mark in collision avoidance, it is the latest feature to be added to systems – autonomous braking – that I believe has the ability to eliminate workplace collisions entirely.
Autonomous braking depends on the plant’s CAN Bus system – its electrical brain – communicating seamlessly with the AI human form recognition technology. If a person enters the red zone (meaning there is a high risk of collision) and the operator fails to respond, the machine will brake automatically. Crucially for operator safety, this braking is intelligent, factoring in the plant’s direction of travel, whether it is loaded, its speed and whether the operator has already started to brake.
By providing the ultimate backup in case of human error, autonomous braking is set to make collisions in the workplace history.
Looking to the future
On our tight, congested UK construction sites, I believe that AI technology with autonomous braking has the potential to completely eliminate collisions. The Construction Industry Training Board’s decision to fit AI collision avoidance systems to all its plants nationwide underlines this. Our next generation of construction professionals will enter the industry with knowledge and understanding of the very best safety practice when it comes to people-plant interface.
Beyond construction, the technology can be fitted to any plants and machinery and its scope in other industries is boundless. Its use is already being explored in mining, demolition, warehousing and waste, and it has recently been installed on forestry wood chippers in Australia.
Clearly, no technology is infallible. But I am optimistic that if AI collision avoidance systems with auto-stop become the norm, we can achieve a year with no fatal injuries as a result of workplace collisions.
Jonathan Guest is CEO of Safety Shield Group
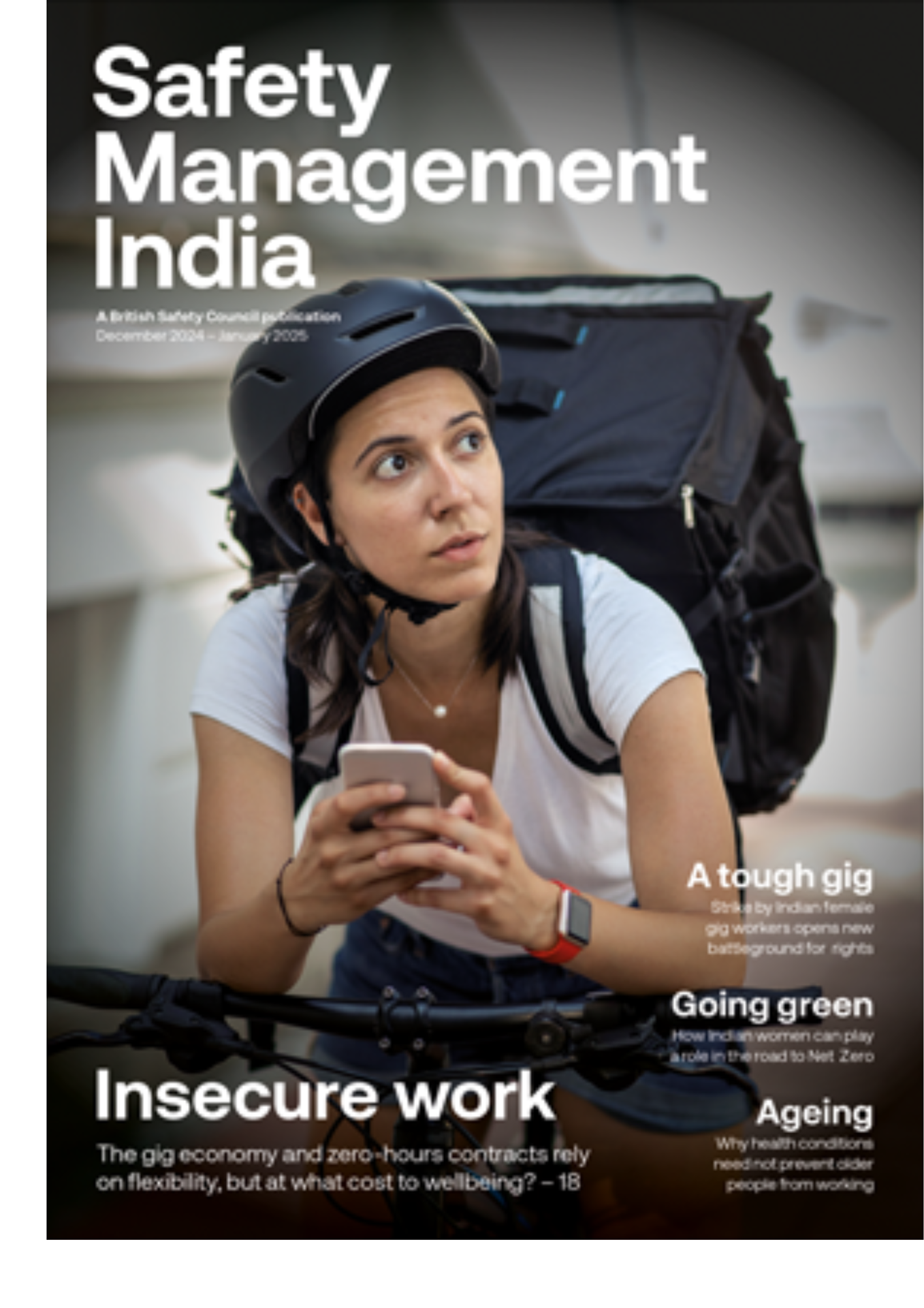

FEATURES
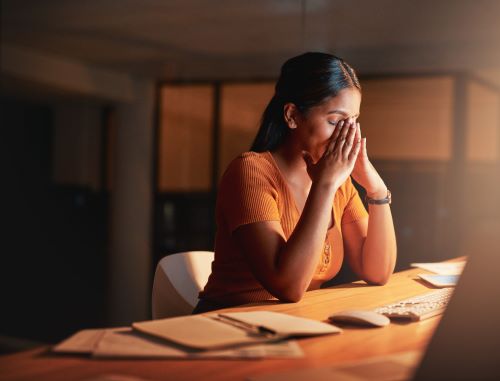
Long working hours in India: debate rages over the impact on wellbeing
By Orchie Bandyopadhyay on 10 March 2025
Calls from high profile leaders of both Indian and global information technology companies for Indian and international workers to work longer hours to boost economic output and speed up the development of AI technology have led to warnings about the threat to workers’ health and work-life balance.
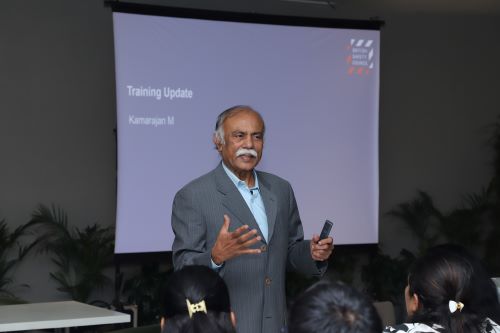
Safety training: top tips for improving its effectiveness
By Marimuthu Kamarajan on 10 March 2025
Health and safety training is a vital tool for improving the safety performance of a business. However, employers must first address any cultural problems that could undermine its effectiveness, such as time pressures encouraging workers to take short-cuts, explains Marimuthu Kamarajan, head of education at British Safety Council.