Exposure to substances like welding fume and metalworking fluids can cause serious and life-threatening diseases, but the risk can be eliminated or reduced through the correct use of controls.
Features
Airborne hazards: a major danger
Manufacturing and engineering are critical to the UK economy. Yet, within these fast-paced and demanding sectors, lie underestimated workplace health hazards; unseen, misunderstood and too often overlooked by employers distracted by navigating tight deadlines and high turnover demands.
Health hazards can arise from exposure to substances such as welding fumes, dust and metalworking fluids. These substances are generated in a number of industries, and each presents health risks that are potentially fatal to workers.
Also, it’s not just a matter of health consequences – overlooking these risks could lead to punitive regulatory fines and lower output as a result of the aforementioned health issues.
So, how can an employer create a safe workplace culture where employees are properly protected from the health risks these substances pose, and keep operations running smoothly?
Welding fumes, dust and metalworking fluids can contain an array of harmful toxic gases, vapours and dusts. Photograph: iStock
What does the science show?
Workers can be exposed to harmful welding fumes, dust and metalworking fluids by inhaling them or through direct skin contact. These substances can contain an array of toxic gases, vapours and dusts – including but not limited to metal oxides, volatile organic compounds (VOCs) and organic and inorganic gases – and prolonged exposure to any of these hazardous materials can result in a wide variety of serious health conditions.
These include respiratory problems, such as silicosis and chronic obstructive pulmonary disease (COPD) and asthma; eye, throat and skin irritation; potential neurological effects and an elevated risk of developing cancers. In fact, a staggering 13,000 deaths per year in Great Britain are estimated to be linked to past workplace exposure to chemicals and dust.
Also, a US study published in October 2022 observed that more than 39,000 workers employed in the motor industry reported incidences of several cancers, including stomach and kidney, due to long-term occupation exposure to metalworking fluids.
As our understanding of the health impacts of industrial exposure to these hazardous substances has grown through scientific research and evidence, there have been corresponding actions from leading bodies.
Notably, the International Agency for Research on Cancer (IARC) found that exposure to mild steel welding fume can potentially lead to lung cancer. Consequently, the Agency classified it as a human carcinogen. This classification also applies to Respiratory Crystalline Silica (RCS), a naturally occurring mineral found in sand, stone, concrete and mortar, which workers can inhale when cutting, drilling, grinding and polishing materials containing these substances.
David Flower: "An occupational hygienist, such as those at IOM, will carry out a thorough risk assessment to understand and assess the threat."
What you need to know about enforcement and current legislation
Regulation 7 of COSHH 2002 states that: “Employers shall ensure that the employee’s
exposure to substances hazardous to health is either prevented or, where this is not reasonably practicable, adequately controlled.”
Therefore, it is clear the onus lies with the employer to protect their workforce, and that negligence around safety standards and control measures designed to prevent exposure will not be tolerated by the authorities.
Recent HSE actions underscore this point. Safety bulletins issued in May 2019 and September 2023 have clearly set out the regulator’s enforcement expectations regarding the use and control of exposure to both welding fume and metalwork fluids by employers. These enforcement warnings and inspection campaigns were prompted by increasing evidence about the dangers these substances pose to health coupled with the fact that there is no known level of safe exposure.
HSE has, in addition, actively focused its attention in recent years on dust and the threat it presents to health. This is due, in the main, to the emergence of more statistics and research on the issue, including research showing that exposure to dust and other hazardous substances leads to approximately 4,000 deaths a year due to cases of COPD.
HSE’s ongoing ‘Dust Kills’ campaign involved more than 1,000 visits to construction sites in just three months in summer 2023 to examine what companies are doing to prevent exposure and protect respiratory health.
Coupled with this are serious consequences for those who fail to adopt the appropriate controls and workplace practices. Recent examples include a West Midlands engineering firm fined £20,000 for failing to protect workers from welding fumes, and a woodworking firm fined £25,000 for dust exposure.
Preventing risk: are you getting it wrong?
“Regardless of duration, HSE will no longer accept any welding undertaken without any suitable exposure control measures in place,” stated HSE in its 2019 Safety Alert, HSE Change in Enforcement Expectations for Mild Steel Welding Fume Bulletin.
Mitigating and preventing exposure to hazardous substances – whether it be welding
fumes, dust or metalworking fluids – involves implementing the correct engineering controls and health surveillance measures.
The control of welding fume exposure depends on the welding process, the nature of the work and the metal being joined. Photograph: iStock
Although many businesses think they are doing this, it is not always the case due to a lack of resources; not fit for purpose, not used as designed and poorly designed, fitted and maintained equipment – such as local exhaust ventilation (LEV) equipment and respiratory protective equipment (RPE); or the absence of any exposure control equipment altogether. Businesses can and do get it wrong.
In order to get things right, it is critical to seek out professional guidance and advice from an organisation such as IOM, who employ a structured approach to workplace risk known as the Hierarchy of Control.
The first step in understanding how to prevent or reduce exposure is to carry out, or commission, a professional and comprehensive risk assessment.
Risk assessment
An occupational hygienist, such as those at IOM, will carry out a thorough risk assessment to understand and assess the threat. Working with your business, an occupational hygienist will look at the specific processes, scrutinise the materials, uncover the potential hazards, identify who might be harmed, and examine what control measures are in place to reduce or eliminate the risk.
For instance, the control of welding fume exposure depends on the welding process, the nature of the work and the metal being joined. Dust is no different, with exposure depending on the source, the concentration and toxicity of the dust, the equipment, the process and the effectiveness of control measures.
To measure airborne contaminants, an occupational hygienist will often combine real-time personal sampling measurements with instant measurements from area/static sampling.
Results will be evaluated with reference to HSE-established exposure limits, as outlined in the document EH40/2005 Workplace exposure limits. The static/area sampling results can be used to assess the effectiveness of the existing and proposed control measures.
Identifying and modifying engineering controls
Using the results, the occupational hygienist will determine the level of risk, consider whether elimination or substitution of the substance is possible to prevent or reduce exposure, and, if not, check if the appropriate engineering control measures are in place to control the risk at source.
For example, is the LEV system designed, fitted and functioning properly? Are the correct isolation measures in place to capture welding fume and prevent wider contamination and exposure? Do employees understand how to clean, test and maintain equipment like LEV and RPE?
As a recent HSE press release on the dangers of metalworking fluids highlights, control measures often fail due to factors such as an absence of LEV, and not completing regular fluid management and health checks.
Focusing on administrative controls
Alongside engineering controls, the occupational hygienist will look at how altering work methods can minimise the risk. This may involve providing enhanced training, raising staff awareness, altering work schedules to limit potential risk and establishing strict protocols on the use of equipment.
Utilising PPE
Although considered the least effective measure, PPE is still a valuable line of defence for workers, and includes the appropriate use and fitting of gloves, eye protection and RPE.
Conclusion
When you underestimate a workplace hazard, or if you overlook it for whatever reason, not only are you placing your employees at risk, but you are also opening your business up to severe regulatory fines and reduced productivity. Making your workplace safe is not based upon a one-size-fits-all solution. What works is a bespoke approach centred upon professional guidance, implementing effective engineering controls, and adopting best practices around education and training.
This approach ensures not only a hazard-free workplace but a culture where safety is important for everyone – from the top to the bottom.
David Flower will be speaking at the SHW Live exhibition in Manchester on 23-24 January on ‘Risks of working with hazardous substances including metalworking fluids’. See: safetyhealthwellbeing.live
David Flower is Senior occupational hygienist at the Institute of Occupational
Medicine (IOM)
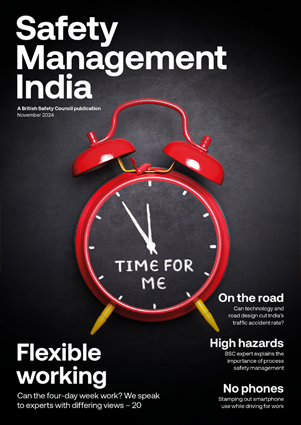

FEATURES
Why changes to recycling legislation in England are an opportunity, not a burden
By on 12 November 2024
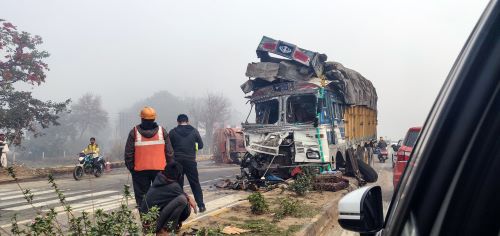
Road safety in India: could better road safety, vehicle technology and enforcement make driving for work safer?
By Orchie Bandyopadhyay on 10 November 2024
India has a poor road safety record, and research shows that commercial vehicles are a major contributor to the problem, with trucks estimated to be the single largest vehicle type involved in impacts leading to fatalities. We look at solutions that could make driving for work and the roads in general safer – from in-vehicle technology that warns truck drivers about unsafe behaviour to improving the design features of major highways.