Breathing in silica dust during tasks like cutting and sanding concrete, rock and stone can cause debilitating and often fatal lung diseases – making it vital employers prevent or reduce exposure.
Features
Breathe more easily
With the news the Health and Safety Executive (HSE) is beginning a targeted inspection initiative in October focusing on British manufacturing businesses where materials that contain silica are used, a growing light is being shed on the dangers posed by exposure to a substance that is estimated to be the second biggest cause of occupational cancer deaths in Britain, after asbestos.
Silica is a natural substance found in most stone, rocks, sand, quartz and clay and in products like bricks and concrete. When these materials are worked on – such as when cutting, sanding, carving and polishing them during construction and demolition, brick and tile manufacturing, stone processing and foundry work – fine, airborne silica dust (known as respirable crystalline silica, or RCS) is released. The dust is often one hundred times smaller than a grain of sand and too fine to see in normal lighting, and can be inhaled deep into the lungs.
Prolonged exposure to RCS can cause lung cancer and other serious, irreversible and often fatal respiratory diseases.
Prolonged exposure to RCS can cause lung cancer and other serious, irreversible and often fatal respiratory diseases. Photograph: iStock
These include silicosis, which makes breathing more difficult and increases the risk of lung infections, and is the most common chronic occupational lung disease globally. RCS exposure can also cause chronic obstructive pulmonary disease (COPD), a group of lung diseases, including bronchitis and emphysema, that result in severe breathlessness, prolonged coughing and chronic disability, and are a leading cause of death globally.
However, although the risk of silica exposure can often be either eliminated or adequately controlled, there remains a lack of awareness of the health risks from RCS among both employers and the workforce, and inadequate working practices that fail to properly control exposure are commonplace.
According to a report published in 2000 by the All-Party Parliamentary Group for Respiratory Health, Silica – The Next Asbestos, at least 600,000 UK workers are exposed to silica dust each year.
So, what is the nature and extent of the threat from silica, which health and safety duties apply and what can businesses can do to mitigate and control the risk of exposure? And how can independent health, safety and occupational hygiene professionals help employers protect workers from silica exposure?
What is the current threat from RCS to workers?
Although the health risks associated with RCS have been known for many years, research commissioned by HSE in 2005 found that silica exposure was responsible for the deaths of around 500 construction workers every year. Meanwhile, many more workers in various industries suffer life-changing and debilitating illness.
The threat from silica remains high despite a raft of campaigns and other actions from organisations such as health and safety regulators and professional bodies over the years. These include:
- IOSH ‘No Time to Lose’ campaign (launched in 2014) aimed at raising awareness among employers of the risks from and ways of preventing occupational cancer, including from silica
- The Unite union’s silicosis register (launched in 2019), which encourages workers who have been exposed to silica dust to register their exposure, to assist with potential future legal cases if they experience long term health problems
- UK MPs and peers on the All-Party Parliamentary Group for Respiratory Health calling in their 2020 report for a variety of measures to reduce the risk from silica – including new health and safety regulations specifically relating to the control of RCS, a major reduction in the UK’s workplace exposure limit (WEL) for RCS (a WEL is a legal limit on the amount of a harmful substances that can be present in the workplace air), and for silicosis to be made a reportable condition under the Reporting of Injuries, Diseases, and Dangerous Occurrences Regulations 2013 (known as RIDDOR)
- The formation of the Construction Dust Partnership, an industry collaboration involving organisations like HSE, safety associations and UK businesses, which aims to help UK construction contractors, employers, operatives and others manage the risk of exposure to dusts and raise awareness of the issue within the construction industry
- HSE’s ‘Dust Kills’ campaign, a collaboration between the regulator and others, such as safety and trade associations, that seeks to raise awareness of the health risks of exposure to construction dust, and recently included a HSE inspection and enforcement campaign in June 2022 looking for examples of poor dust exposure control by employers on British construction sites.
Since 2013, silicosis is no longer a notifiable (i.e. reportable) disease under the UK’s RIDDOR reporting regulations, making it hard to track and assess the problem nationally. Photograph: iStock
There are several reasons why exposure to silica dust remains a problem in British workplaces:
- Employers failing to understand the health risks from – and therefore the need to prioritise – the control of exposure to RCS
- Poor awareness among workers, both of the respiratory health risks from RCS and the appropriate control measures they should follow to prevent themselves and co-workers being exposed – this is due in part to the lack of communication, training and awareness on RCS risks and precautions provided by employers
- A culture where dust is seen as an expected and normal part of the job, particularly short-term exposure
- The extensive use of power tools (like concrete breakers and rotary tools for cutting and polishing stone), but a poor understanding of the importance of measures like using on-tool air extraction to capture silica dust at source to prevent it being breathed in; using on-tool water suppression to reduce dust emissions; and adopting other control measures, such as the use of local exhaust ventilation, like an enclosed booth that extracts dust from the air
- An over-reliance on respiratory protective equipment – such as respirators – as the main control measure
- The size and spread of the UK construction industry – construction work is often transient, with sites and locations changing regularly, and many construction workers are employed by small businesses or are self-employed, all of which can make it difficult for HSE to carry out inspections and enforcement on poor silica controls by employers
- Since 2013, silicosis is no longer a notifiable (i.e. reportable) disease under the UK’s RIDDOR reporting regulations, making it hard to track and assess the problem nationally
- Occupational lung diseases caused by RCS exposure – such as silicosis and lung cancer – have a long latency, which mean workers will not immediately experience or notice ill health symptoms that could indicate the harm silica is causing to their respiratory health
- Employers avoiding investing in exposure control equipment for financial reasons – for example, the price of face masks has increased due to the pandemic.
In addition, countries around the globe – including Australia and the USA – are seeing a significant rise in cases of occupational silicosis.
However, the increase is not being seen in occupations traditionally associated with the disease – like construction, foundries or manufacturing of items like stone fireplaces, bricks and tiles. Instead, the rise in cases seems to be driven by the growth of modern industries where silica is used or silica dust created. These include domestic kitchen and other worktop production (which are often made from stone or stone composites), denim sandblasting during the production of clothing and jewellery polishing.
Silica is being introduced, used and worked on in these industries but workers are not being given adequate information and training on the health risks and exposure controls to follow. Also, the employers themselves have little understanding of the need for exposure controls like on-tool extraction and suitable RPE.
Which health and safety duties apply in the UK?
Unlike asbestos, there is no specific standalone set of UK regulations setting out duties for employers to prevent or adequately control of exposure to RCS at work. Instead, employers have a general duty to prevent – or adequately control – exposure to RCS under the Control of Substances Hazardous to Health Regulations 2002 (COSHH).
In essence, employers are required under COSHH to eliminate employee exposure to RCS – or, if this is not practicable – to reduce RCS exposure to as low a level as reasonably practicable.
This means taking steps such as:
- Assessing the risk of workers being exposed to silica dust
- Carrying out regular testing – for example, air sampling may be required to assess the level of silica dust in the air to check the exposure controls are adequate or need improving and to ensure the Workplace Exposure Limit for RCS is not being exceeded
- Choosing effective control measures – such as suppressing silica dust using water spray systems on hand-held power tools, using on-tool extraction systems to remove dust as it is being produced and using fixed, enclosed booths with air extraction systems to capture and remove RCS
- Regularly monitoring and reviewing the effectiveness of the control measures
- If exposure cannot be eliminated or adequately controlled using engineering methods, providing adequate and suitable RPE, such as respirators and dust masks
- Raising awareness of the health risks of RCS exposure – and how to prevent it – through education and training for employees.
In the UK, the WEL for RCS (the maximum allowed concentration in the workplace air), is 0.1 mg/m³, averaged over eight hours), which is higher than in countries like Australia, Canada, Finland and Italy.
HSE guidance also states that employer must consider providing health surveillance for silicosis for workers involved in high-risk occupations, including construction, foundry work, manufacturing, quarries and stonework. The guidance also states that (in general) if workers are regularly exposed to RCS dust and there is a reasonable likelihood that silicosis may develop, health surveillance must be provided.
Craig Lewis is senior occupational hygienist at the Institute of Occupational Medicine (IOM)
If HSE inspects a work site and discovers problems like a failure to adequately reduce exposure to RCS, or breaches of the WEL for silica, it can take enforcement action such as issuing prohibition and enforcement notices requiring work to either be stopped or the exposure controls improved. It can also prosecute employers for failing to control RCS exposure, resulting in significant fines.
HSE can also require a negligent employer to cover the costs of its investigation, and any resulting enforcement action, under the Fee for Intervention (FFI) scheme. Therefore, fines for breaching safety law and charges levied under FFI can be damaging for a business, both financially and reputationally.
For example, a Lancashire-based company was recently fined £20,000 for putting employees’ health at risk due to RCS exposure and for failing to implement adequate silica control measures.
What does the science show?
Although the risk of lung damage from silica has long been known, it was only in 1997 that the International Agency for Research on Cancer classified silica as a human carcinogen and ‘capable of causing cancer and/or heritable genetic damage’.
Long term exposure to silica dust results in the substance becoming deposited in the lungs and its toxicity makes it difficult for the body to remove it. RCS causes persistent lung inflammation over years, and swelling and scarring of the lung tissues, known as fibrosis.
In the early stages of silicosis there are often no symptoms, but as the disease gets worse there is shortness of breath and eventually individuals may find it difficult to walk short distances. The condition is progressive, so even if an individual is no longer exposed, the effects of silicosis are irreversible and continue to develop.
Silicosis is split into three distinct types:
- Acute silicosis – this is caused by rapid and intense exposure to RCS over a brief period of time (the condition generally appears within five years)
- Accelerated silicosis – this develops after five to 10 years of exposure to RCS
- Chronic silicosis – this is caused by exposure over a prolonged period of more than 10 years.
There are currently no effective medical treatments for silicosis and the condition can prove fatal in some cases through respiratory failure.
As a result, it is crucial that employers implement adequate and suitable control measures to reduce the risk of silicosis and lung disease, and the starting point should be undertaking a COSHH risk assessment.
In workplaces where it is impossible to eliminate the risk of RCS exposure, employers must assess, manage and control the risk of exposure to as low a level as possible.
If an employer lacks the necessary in-house expertise, an independent occupational hygiene consultant can help them to implement and follow the hierarchy of control for RCS.
Risk assessment
Employers need to assess the risk of exposure to RCS and whether their existing control measures are adequate are more needs to be done to protect employees from risk to their health.
One effective way of checking employees’ exposure to RCS in the workplace air – and deciding if the exposure controls are adequate or need improving, and whether the WEL is being complied with – is to commission an occupational hygiene expert to carry out exposure measurements, known as air sampling.
By using scientifically proven methods like personal sampling exposure (taking an air sample near the worker’s breathing zone to measure the amounts of silica inhaled for a specific task), an occupational hygiene expert can assess the level of risk from RCS and advise the employer if their exposure controls are adequate, or if improvements must be made.
Engineering controls
Depending on the results of the risk assessment, employers may need to change the way tasks are carried out to eliminate or reduce the risk of RCS exposure.
Employers should always seek to control RCS at the source, as this will help protect both those workers who are directly exposed – such as someone operating a concrete cut-off saw – and others who may be present nearby and could inhale the dust.
Effective engineering controls that can help to prevent or adequately reduce RCS exposure include:
- Local exhaust ventilation (LEV) systems to capture and remove contaminated air – such as an enclosed booth with an air extraction system
- Water to suppress dust during tasks like cutting concrete paving blocks or chiselling or polishing stone using powered hand-held tools – such as on-tool water suppression systems, or fitting water suppression systems on fixed machinery like CNC machines using for the automated boring and polishing of stone using rotary tools
- Using vacuum equipment to clean silica dust off work surfaces and machinery instead of dry sweeping, which increases the risk of inhaling RCS
- On-tool extraction, a type of LEV system that fits directly onto the tool to remove dusts as it is produced.
Personal protective equipment
Personal protective equipment, such as respirators, should be provided if engineering controls alone are inadequate to control the risk. However, RPE will only be effective in reducing the risk of exposure if it is properly selected, maintained, cleaned and fitted, and if workers are given appropriate training on its correct use. For example, workers must have a face-fit test for a tight-fitting respirator and be clean shaven when using RPE that relies on a tight fitting seal to the face, otherwise RCS can leak into the mask and be inhaled.
How can workers protect themselves?
Although employers must take all reasonably practicable measures to protect workers from RCS exposure, employees also have a role to play in looking after their own health when working with substances containing silica. For example, workers should be given suitable health and safety information, training and supervision so they understand how to:
- Use toolbox meetings and talks to raise any questions about RCS risks and exposure controls
- Correctly follow all control measures
- Correctly wear the appropriate RPE and inform supervisors if it becomes damaged or faulty
- Wear protective clothing properly
- Follow good housekeeping rules and personal hygiene measures such as handwashing, care and maintenance of RPE, and safe handling and disposal of materials.
However, despite the serious nature of the risk from RCS, stakeholders like HSE, safety associations and many businesses continue to raise awareness and promote good practice to reduce the risk of exposure to RCS at work in the UK.
For example, the recent Tideway Tunnel project under the Thames made a concerted and successful effort to reduce exposure to silica dust, from the design phase onwards. This involved collaborative working across the project between occupational hygienists and the environmental teams.
However, RCS presents a very real risk to workers in industries like construction, brick and tile manufacturing and stone processing, and it is only through suitable education, compliance and the adoption of effective risk controls that any positive change will come about.
Craig Lewis is a senior occupational hygienist within the Institute of Occupational Medicine’s Workplace Protection team, who use a mix of ventilation and occupational hygiene services to protect hospital patient and workplace employees’ health. A veteran occupational hygienist, Craig has been practicing for over 17 years and has an in-depth working knowledge of industry issues and client challenges. For more information see: iom-world.org
Nathan Baker, chief executive of IOM, will be chairing a discussion with other IOM health and safety experts on ‘Looking after the whole worker: what the latest scientific research means for you and your workplace’, at the British Safety Council’s annual conference on 14 October in London. Book at: https://www.britsafe.org/awards-and-events/events/past-conferences/british-safety-council-12th-annual-conference
For HSE’s guidance on silica see: hse.gov.uk
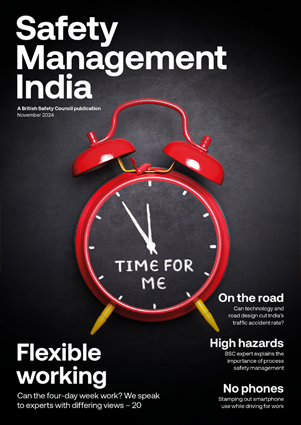

FEATURES
Why changes to recycling legislation in England are an opportunity, not a burden
By on 12 November 2024
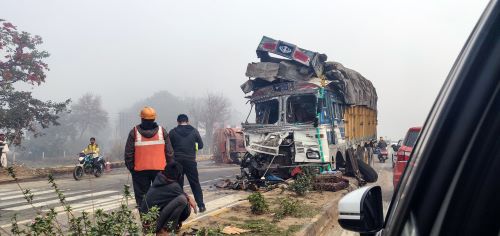
Road safety in India: could better road safety, vehicle technology and enforcement make driving for work safer?
By Orchie Bandyopadhyay on 10 November 2024
India has a poor road safety record, and research shows that commercial vehicles are a major contributor to the problem, with trucks estimated to be the single largest vehicle type involved in impacts leading to fatalities. We look at solutions that could make driving for work and the roads in general safer – from in-vehicle technology that warns truck drivers about unsafe behaviour to improving the design features of major highways.