Several thousand workers in India’s automotive parts factories suffer horrendous hand and finger injuries every year. Campaigners say it’s time the country’s biggest automotive companies do more to improve health and safety standards in their supply chain.
Features
Driving into danger
In February, a 44-year-old welding worker at the Chakan plant of Automotive Stampings and Assemblies Ltd (ASAL), an automobile component company, was killed after he was hit on the head and neck by an arm of a robotic machine that fell on him. Investigations revealed that the accident occurred due to a possible snag in a sensor. Umesh Ramesh Dhake had been working with the company for the past 22 years.
His wife, who works as a domestic help, has lodged a first information report (FIR) against five officials of the multinational, including some department officials and supervisors responsible for health and safety measures. The complaint alleges that adequate safety measures were not taken, and her husband was not wearing a helmet or any other safety gear at the time of the accident.
A spokesperson for Automotive Stampings and Assemblies said: “At ASAL, we do lay the utmost importance on safety and mandate that each and every workmen and employee adhere to safety norms and wear appropriate PPEs while working at the shopfloor. This was an extremely unfortunate incident that the deceased was not wearing a helmet at the time of the accident. We are investigating the causes that led to the incident.”
Dhake’s death has devastated his co-workers and family. A worker at ASAL said: “It is an injustice because he was not responsible for his accident.”
Whether assembling cars, stamping out automotive bodies or making vehicle parts, an automotive plant is a dangerous place to work in India. Employees and workers in automotive plants are exposed to a variety of hazards, such as: chemicals, burns, heavy/rotating machinery, sharp objects, slippery surfaces, vapours and fumes, slips, trips and falls and loud noises. These hazards can result in serious injuries or even death.
Workers are suffering terrible hand injuries in India's car part factories in Gurgaon-Manesar. Photograph: Safe in India Foundation
Workers are also at risk of developing sprains, strains and injuries due to heavy lifting or maintaining awkward postures for long periods of time.
Even Covid-19 infection protocols, such as physical distancing, are not always followed at automotive manufacturing plants.
Poor Covid infection controls
When India was hit by a huge second coronavirus wave, Renault Nissan India and workers at its plant in Tamil Nadu were locked in a legal tussle after workers petitioned the Madras High Court in May to halt operations at the site. The workers alleged that physical distancing norms were being flouted and company-provided health benefits were outweighed by the risk to their lives.
In response, the Franco-Japanese car manufacturing joint venture, which has its headquarters near Chennai, said in a court filing that there was a “compelling need” to continue operations to fulfil domestic and export orders. It said all Covid-19 infection prevention norms were being followed.
The union body, Renault Nissan India Thozhilalar Sangam (RNITS), which represents all 3,500 permanent factory workers employed at the Tamil Nadu plant, demanded that physical distancing protocols must be followed. They also called for the management to take responsibility for any risks to the workers or their family members.
The factory employs 3,000 contract workers, 2,500 staff members and 700 apprentices.
In early June, an interim peace deal was signed between the company and its workers’ union that involves attempting ways of maintaining social distancing on the factory floor, said a top union leader.
Accordingly, the management and the union agreed to the ‘empty pitch ratio’ of 3:1 in the trim and chassis and body shop.
“Simply put, after three cars in the conveyor belt, one slot will be empty so that a worker need not move to the next workstation to complete his work,” K.Balaji Krishnan, president of RNITS told IANS newswire.
M Moorthy, general secretary of RNITS, said the agreement meant vehicle production will be reduced from 40 to 30 cars an hour.
Later in the month, the court directed officials to visit the factories of car manufacturers near Chennai, including that of Renault-Nissan, to put in place uniform Covid-19 guidelines, such as maintaining physical distancing between workers in the premises.
Chennai, aka the ‘Detroit Of India’, is a hub of automobile manufacturing facilities for leading carmakers, like Ford, Hyundai, Nissan/Renault/Datsun, Royal Enfield and a few more. It is home to around 35–40 per cent of India’s total automobile industry.
Injuries in the automotive parts sector
Another major automobile manufacturing area outside Delhi is the Gurgaon-Manesar automotive hub, which houses the factories of Hero MotoCorp, Maruti Suzuki, Yamaha, Escorts, JCB, Honda Motorcycle and Scooter India and Suzuki Motorcycle India. It also has a huge number of parts suppliers that employ thousands of workers.
Unfortunately, the hub is witnessing a significant number of accidents in the factories of small automobile component manufacturing companies, according to the Safe In India Foundation (SII). This is a non-profit organisation that supports injured workers and lobbies for improved safety standards in Gurgaon-Manesar’s automotive component factories.
SII says there is a big chain of Tier 1, 2, and 3 suppliers, who manufacture automotive parts for supply to automotive companies higher up the chain. Awareness of health and safety is more lax and accidents are more frequent lower in this chain.
SII has documented 1,369 cases of serious injuries that workers have suffered so far, and the number is still rising at the rate of two per day. Of these, 548 people have lost at least a finger, 234 have lost two, 133 have lost three, 73 have lost four and 17 have lost all five.
Fifty-nine per cent of the accidents took place on machines called power presses, which cut, shape or mould metal by ramming it with a heavy piston-like arm. A power press can trap arms, wrists or fingers, causing serious injuries. In such accidents, which are known as crushing injuries, workers can lose their fingers and/or hands.
“SII has found and assisted more than 500 such workers every year in the 2017-2021 period, just in Gurugram-Manesar with a small outreach team of three,” the organisation said. “Many injured workers are too scared of their employers/contractors to talk to SII freely and therefore SII cannot record their information.”
Photograph: iStock/kadmy
Preventable hand crush injuries
SII states these injuries are preventable. Companies at the bottom of the value chain, where most of these accidents happen, operate at much lower margins and tend to cut corners wherever possible. The safety of their workers is not their top priority.
“Lack of awareness is the biggest issue,” says Sandeep Sachdeva, the co-founder and CEO of SII. “Companies need to be made aware about safety mechanisms in the machines, proper training of the workers before they operate dangerous machines and provision for safety gear. Working in a factory and on the shopfloor has occupational hazards and accidents can happen but excessively long hours under tremendous production pressure enhances the chances of an accident.”
In its report, SafetyNiti 2021, SII provides a top-down analysis of the publicly available occupational safety and health (OSH) policy documents of the top 10 automotive brands in India.
Inadequate OSH policies
Experts say the large automotive brands’ OSH policies and practices are currently inadequate to promote and ensure worker health and safety in their deeper supply chain.
“Without improving these policies and their implementation urgently, we cannot expect a reduction in these accidents that are maiming thousands of workers every year,” said Sachdeva from SII. “On the other hand, if we can get this right, given that the Indian auto sector is about half of the Indian manufacturing GDP, this will have a positive spillover effect on all Indian manufacturing and thereby on Indian labour productivity, which, ranked at 115, is one of the lowest in the world.”
SII reviewed the publicly available documents of 10 automotive brands, namely Ashok Leyland, Bajaj Auto, Eicher Motors, Hero MotoCorp, Honda Motorcycles and Scooters India, Hyundai Motor Company India, Mahindra and Mahindra, Maruti Suzuki India, Tata Motors and TVS Motor Company. Automotive companies have a moral responsibility to ensure there are adequate health and safety standards in their entire supply chain, argues SII.
The report states that the OSH policies of most original equipment manufacturers (OEMs – i.e. the biggest automotive brands), do not explicitly state that they cover contract/casual/temporary workers in their own, ‘in-house’ factories. Also, none of the OEMs has a standard operating procedure or an OSH implementation plan for their deeper supply chain. None of the OEMs appears to have a stated human rights policy in the public domain, although they mention “respect human rights”, or similar language, in some of their other documents, says SII.
Of the 10 OEMs, SII found the publicly available OSH-relevant policies of Maruti Suzuki, Tata Motors, and Mahindra to be relatively better in their coverage of OSH. However, SII says these three companies also have considerable ground to cover, particularly with regards to their deeper supply chain.
SII’s report is an outcome of its analysis of factory accidents and research into the policies and practices of India’s largest OEMs, or auto giants. Among its main observations on the policy framework is that the health and safety policies of most of the automotive majors don’t explicitly say they cover contract/casual/temporary workers in their own factories. SII adds that seven out of the 10 companies don’t have a supplier code of conduct that aligns with the National Guidelines for Responsible Business Conduct (NGRBC).
Contracted and migrant workers at greater risk
According to the SII report, nearly 90 per cent of the injured workers that SII assisted and analysed were migrants, primarily from Uttar Pradesh, Bihar and Odisha. Of them, 65 per cent were contractual workers and 95 per cent were not affiliated with any trade union that could fight for their rights.
SII recommends that contract workers in factories should have identical OSH policies as permanent workers; creating, and making available in the public domain, a supplier code of conduct that includes OSH; and creating, and implementing, a standard operating process and an OSH implementation plan for the deeper supply chain.
Arun Maira, a former member of the Planning Commission of India, writing in the foreword to the SafetyNiti 2021 report, said: “Indian auto-companies produce world class products and have made India proud… the companies may publicly espouse respect for human beings and their rights; the reality as the report reveals, is different. It reveals a disrespect for the lives of workers and the conditions in which they work.
“The OEMs are role models. They must demand respect for human safety in all enterprises in their extensive supply chains.”
Industry experts point to a serious under-reporting of such accidents by the automotive parts manufacturing plants in the lower part of the industry’s supply chain. They say this is one of the reasons why a systemic response cannot be formulated to address the issue. Inspections of factories and industrial units have also fallen, and the penalties for safety violations are very low, they add.
Emphasising that ensuring the health and safety of workers will directly boost the automotive sector’s productivity by avoiding the loss of skilled workers due to injuries (and therefore helps boost economic growth and social development), Rajesh Menon, director general of the Society for Indian Automobile Manufacturers, said that appropriate measures must be taken to avoid such accidents at all levels.
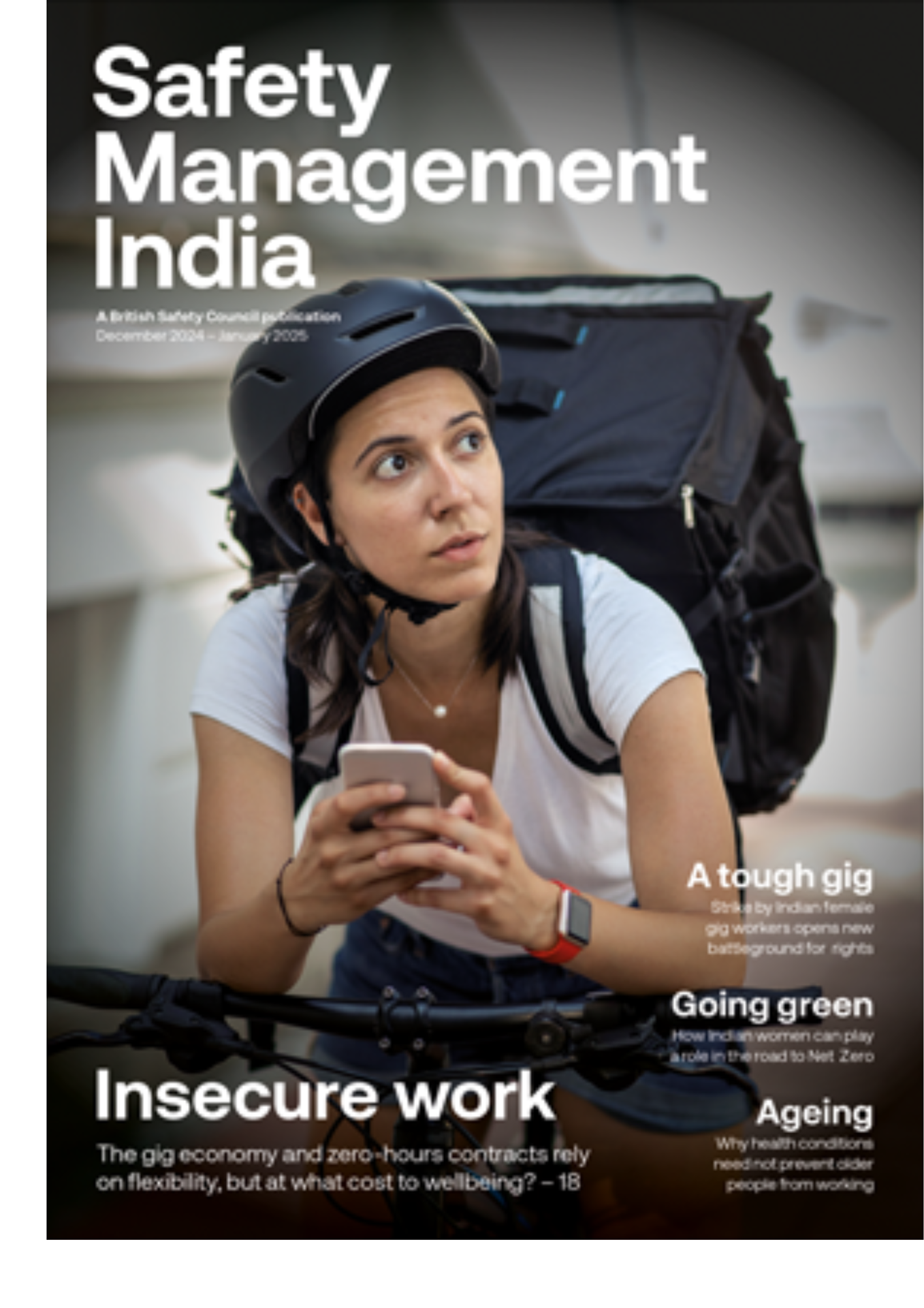

FEATURES
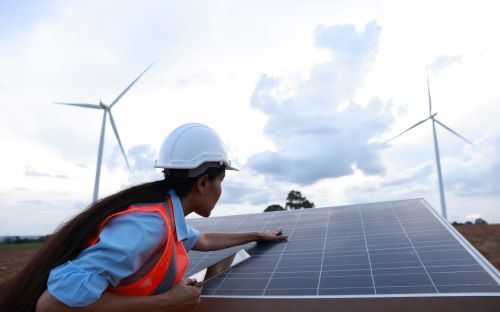
India’s path to net zero: a work in progress
By Orchie Bandyopadhyay on 08 April 2025
India is implementing a variety of clean energy measures to hit its target of net zero greenhouse gas emissions by 2070, including plans to rapidly scale up the generation of nuclear power. However, climate experts say significant finance will be required from developed countries to phase out coal power, accelerate renewables deployment and expand the national electricity grid.
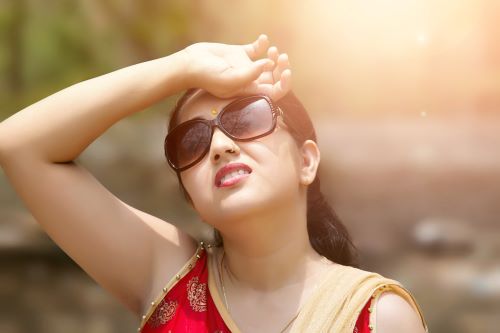
Too hot to handle: early arrival of heatwaves in India sparks calls for action to protect workers and the public
By Orchie Bandyopadhyay on 08 April 2025
Temperatures in India in February 2025 were the hottest since records began over a century ago, prompting warnings the country needs to urgently step up efforts to protect both workers and the general population from the health risks posed by extreme heat and humidity.